Medium-Pressure 16-25 MPa Hydraulic Gear Pump - Efficient And Stable Operation, Reducing Maintenance Costs And Improving Production Efficiency
Fairy Deer Benefits Of 16 - 25 MPa Medium-pressure Hydraulic Gear Pump
Rated pressure range of 16-25 MPa, suitable for diverse hydraulic applications;
Compact and durable design for easy integration and extended operational reliability;
Efficient hydraulic performance with low pulsation and smooth flow;
Available in various displacements to match your system requirements;
Compliant with international standards for quality and safety;
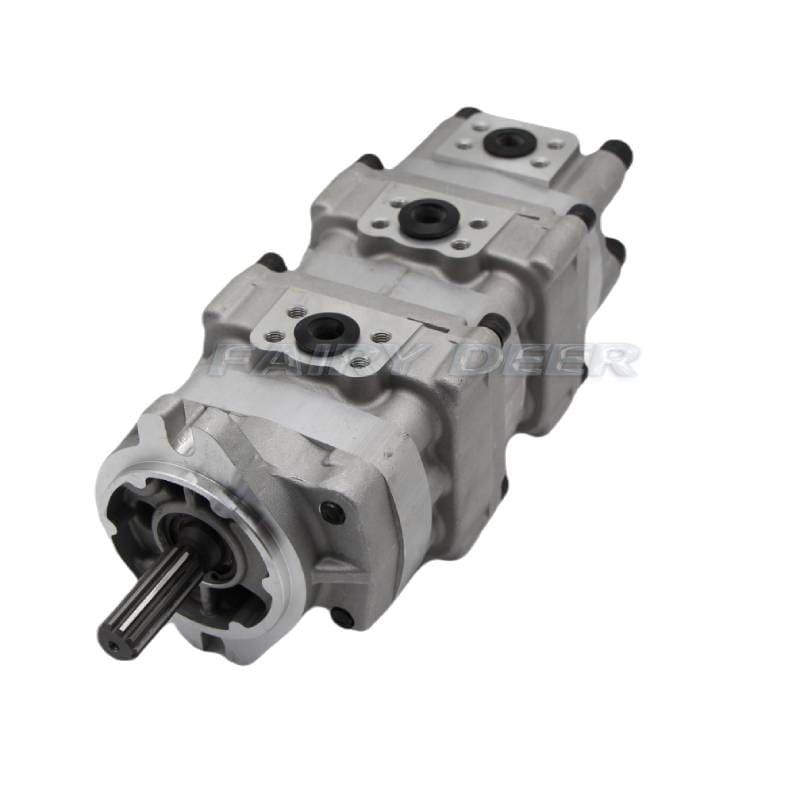
COMPARISON
Optimized Pressure Range for Versatility:
Medium-pressure gear pumps operating at 16-25 MPa provide an ideal balance between power and durability, suitable for a wide range of industrial, agricultural, and mobile machinery applications where extremely high pressure is unnecessary.
Lower Operating Stress and Longer Service Life:
Compared to high-pressure pumps (>25 MPa), 16-25 MPa pumps experience less mechanical and hydraulic stress, resulting in improved longevity and reduced maintenance costs.
Compact and Lightweight Designs:
Many medium-pressure gear pumps use aluminum or lightweight materials, making them easier to install and integrate into existing hydraulic systems without significant weight or space penalties.
Efficient and Reliable Performance:
These pumps maintain stable flow rates with low noise and vibration, enhancing system efficiency and operator comfort, especially in mobile equipment such as forklifts, loaders, and small excavators.
Cost-Effectiveness:
Medium-pressure pumps generally have lower manufacturing and operational costs compared to high-pressure units, offering customers a more economical solution without compromising reliability.
Wide Application Scope:
16-25 MPa pumps are well-suited for material handling, construction machinery, agricultural equipment, and industrial vehicles, covering most common hydraulic needs without the complexity of high-pressure systems
Higher Pressure Capacity for More Demanding Applications:
Medium-pressure gear pumps rated at 16-25 MPa offer significantly higher pressure capabilities than low-pressure pumps (<16 MPa), enabling them to power more complex and heavy-duty hydraulic systems such as forklifts, loaders, agricultural machinery, and industrial vehicles.
Better Efficiency and Performance Stability:
Operating at medium pressure allows these pumps to maintain stable flow rates and higher volumetric efficiency under moderate to heavy loads, reducing flow pulsation and system vibration compared to low-pressure pumps.
Robust Construction for Durability:
Medium-pressure pumps often use materials like aluminum combined with advanced internal gear designs, ensuring a strong yet lightweight structure that withstands higher mechanical stresses and extends service life.
Broader Application Range:
While low-pressure pumps are suitable for simple hydraulic tasks with lower force requirements, 16-25 MPa pumps cover a wider range of industrial and mobile equipment needs, providing a cost-effective solution without the complexity of high-pressure (>25 MPa) systems.
Reduced Maintenance and Longer Service Intervals:
Due to optimized pressure levels, medium-pressure pumps suffer less wear and tear than low-pressure pumps working near their upper limits, resulting in fewer breakdowns and lower maintenance costs.
Ease of Integration and Installation:
Medium-pressure gear pumps typically feature standardized flanges and shaft types (e.g., A-type elliptical flange, flat key shaft), facilitating quick and reliable installation in existing hydraulic systems.
External Gear Pumps (Outer Gear Pumps) Advantages:
Simple and Compact Structure: External gear pumps have a straightforward design with fewer moving parts, which leads to reliable operation and easier maintenance.
High-Speed Operation and High Flow Rates: Small external gear pumps can run up to 4000 rpm, achieving high flow within a compact size, suitable for applications requiring steady, smooth, and reversible flow.
Self-Priming Capability: They can self-prime effectively, making them ideal for systems where suction conditions vary or fluid supply is intermittent.
Wide Material Compatibility: External gear pumps are available in various materials (cast iron, stainless steel, composites) to handle corrosive and abrasive fluids, enhancing durability and application range.
Cost-Effective and Easy to Manufacture: Their simpler gear geometry (e.g., spur gears) makes manufacturing easier and costs lower, suitable for budget-conscious projects.
Low Noise Operation with Helical or Herringbone Gears: Using helical or herringbone gears reduces noise and vibration, improving operator comfort in noise-sensitive environments.
Internal Gear Pumps (Inner Gear Pumps) Advantages:
Excellent for Viscous Fluids: Internal gear pumps handle high-viscosity liquids (oils, chemicals) efficiently with lower energy consumption, making them ideal for chemical, lubrication, and food industries.
Smooth, Pulsation-Free Flow: Their design provides very stable and continuous flow with minimal pulsation, critical for precision dosing and metering applications.
High Pressure Capability and Long Service Life: Internal gear pumps generally withstand higher pressures with less wear, offering longer operational life and reliability.
Multi-Output and Flexible Operation: Advanced internal gear pumps can offer multiple independent outputs from a single pump body, allowing complex hydraulic circuit designs and flow control.
Quieter and Less Vibration: Due to internal gear engagement, these pumps operate with less noise and vibration compared to many external gear pumps.
Recommended Medium-pressure Gear Pump
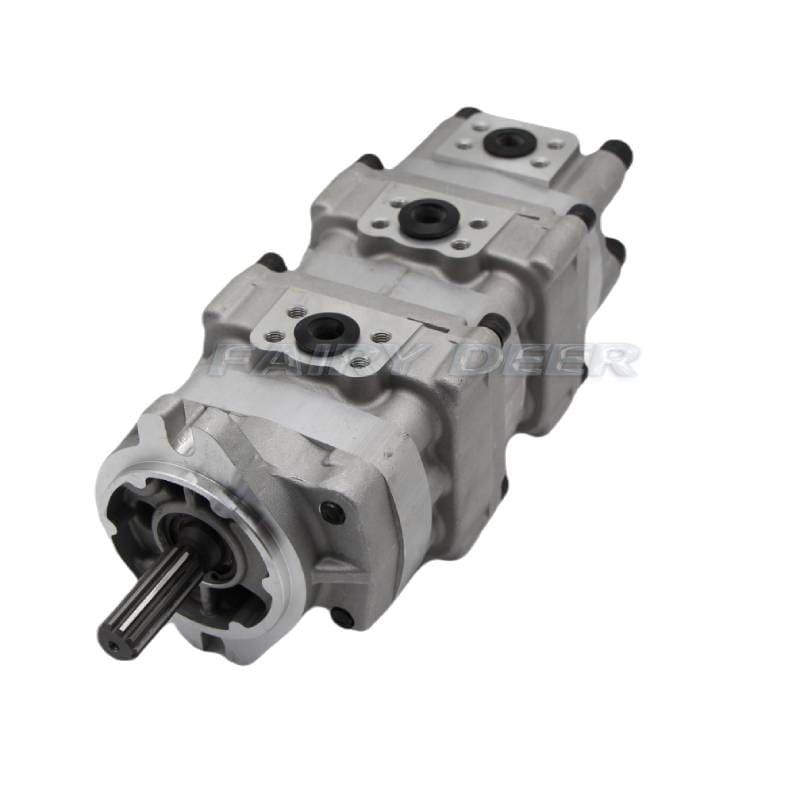
Single Gear Pump For KOMATSU PC75UU-2 Excavator
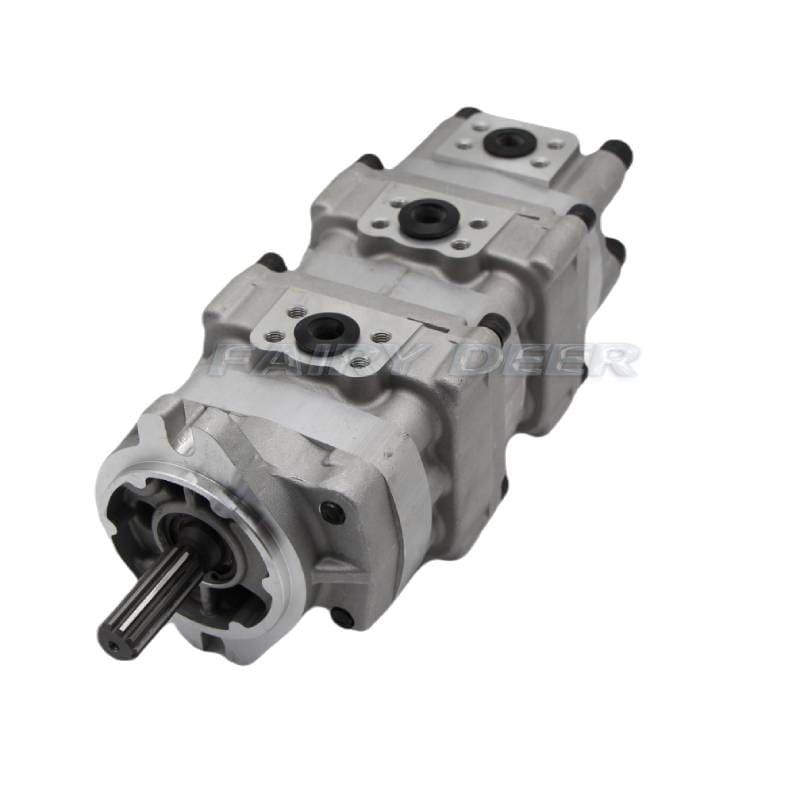
Double Gear Pump For CATERPILLAR E305.5 E306 E308 Excavator
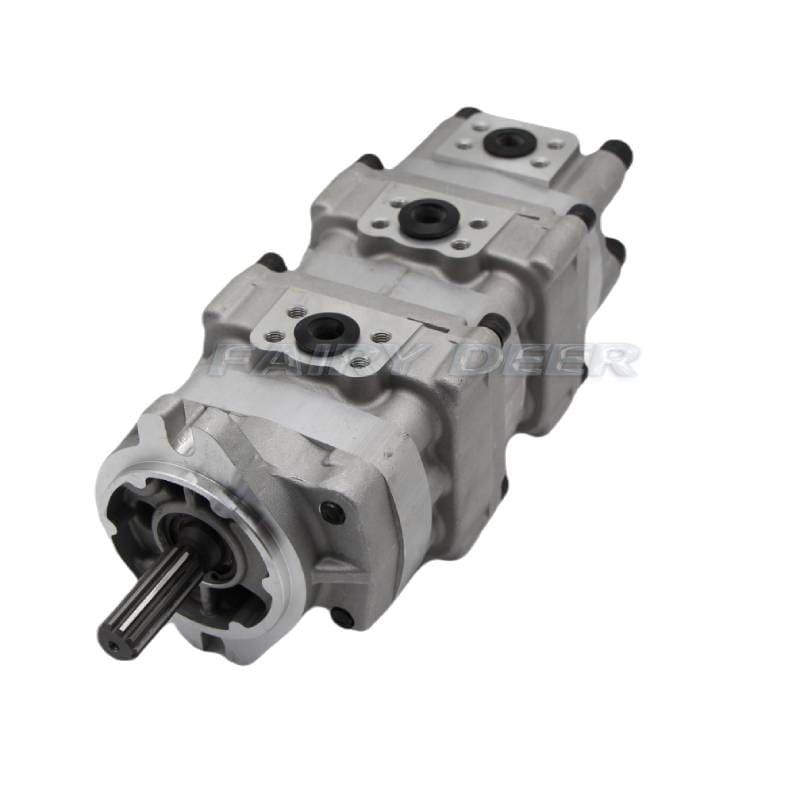
Triple Gear Pump For KOMATSU 3-5 Ton Excavator
Medium-Pressure Hydraulic Gear Pumps: Efficient And Stable Power Solution For Multiple Industries
Discover our 16-25 MPa medium-pressure hydraulic gear pumps, engineered for diverse industries including material handling, construction machinery, agricultural equipment, and industrial vehicles. Experience reliable pressure output, energy-efficient operation, and durable performance that ensure your hydraulic systems run smoothly and cost-effectively every day.
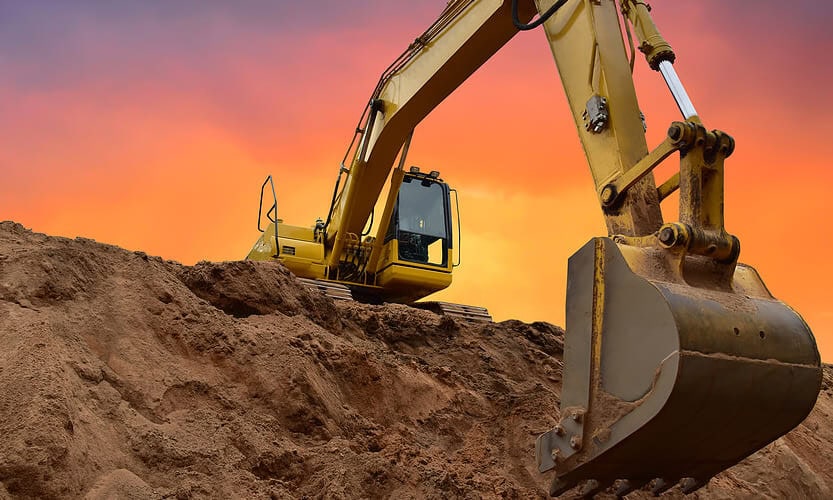
Construction Machinery - Excavator
Powering hydraulic arm, swing motor, and travel system.
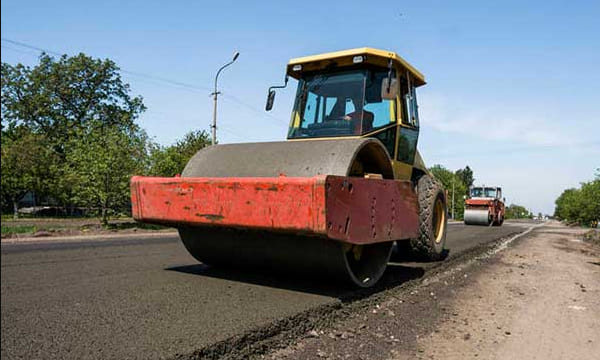
Construction Machinery - Road Roller
Powering vibration system and steering hydraulic.
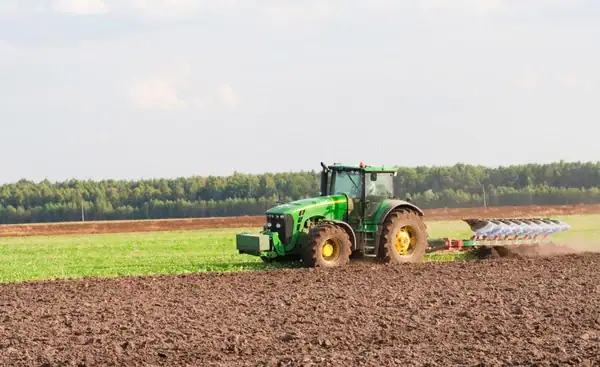
Agricultural Machinery - Tractor
Powering hydraulic hitch and implements like plows.
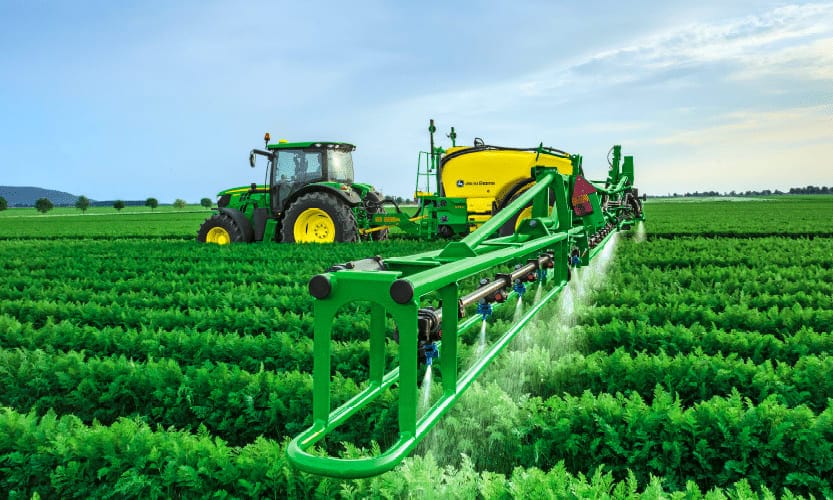
Agricultural Machinery - Sprayer
Controls boom lifting and liquid pump operation.
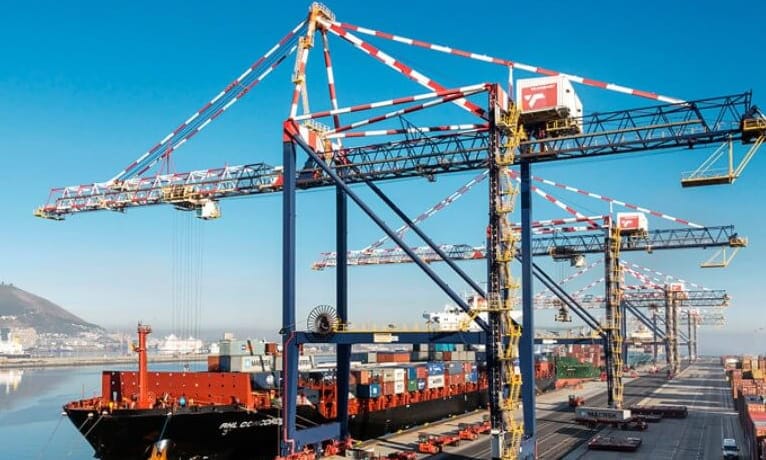
Material Handling Equipment - Port Crane
Supports container lifting and slewing.
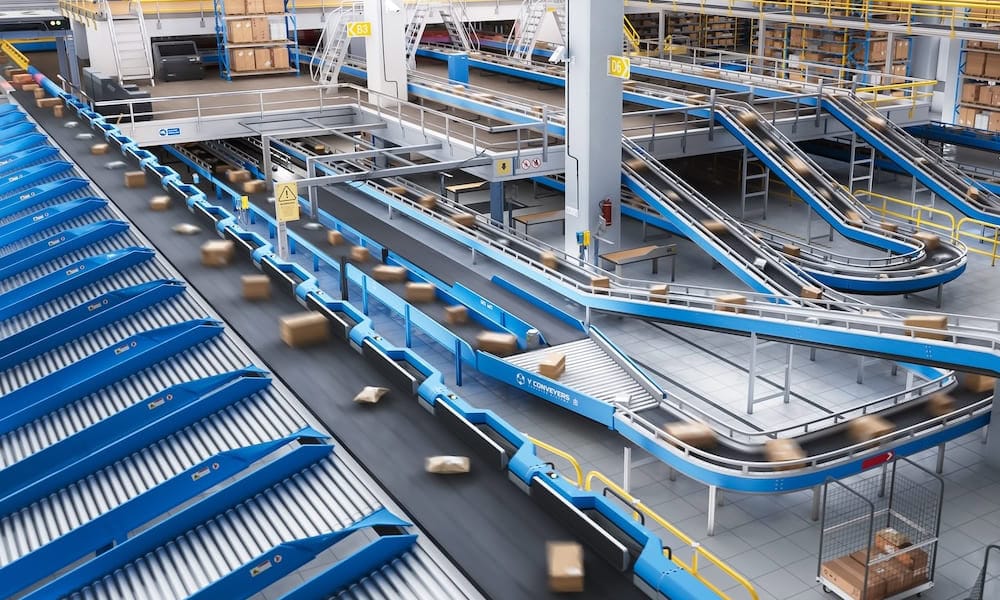
Material Handling Equipment - Conveyor System
Provides power for hydraulic motors.
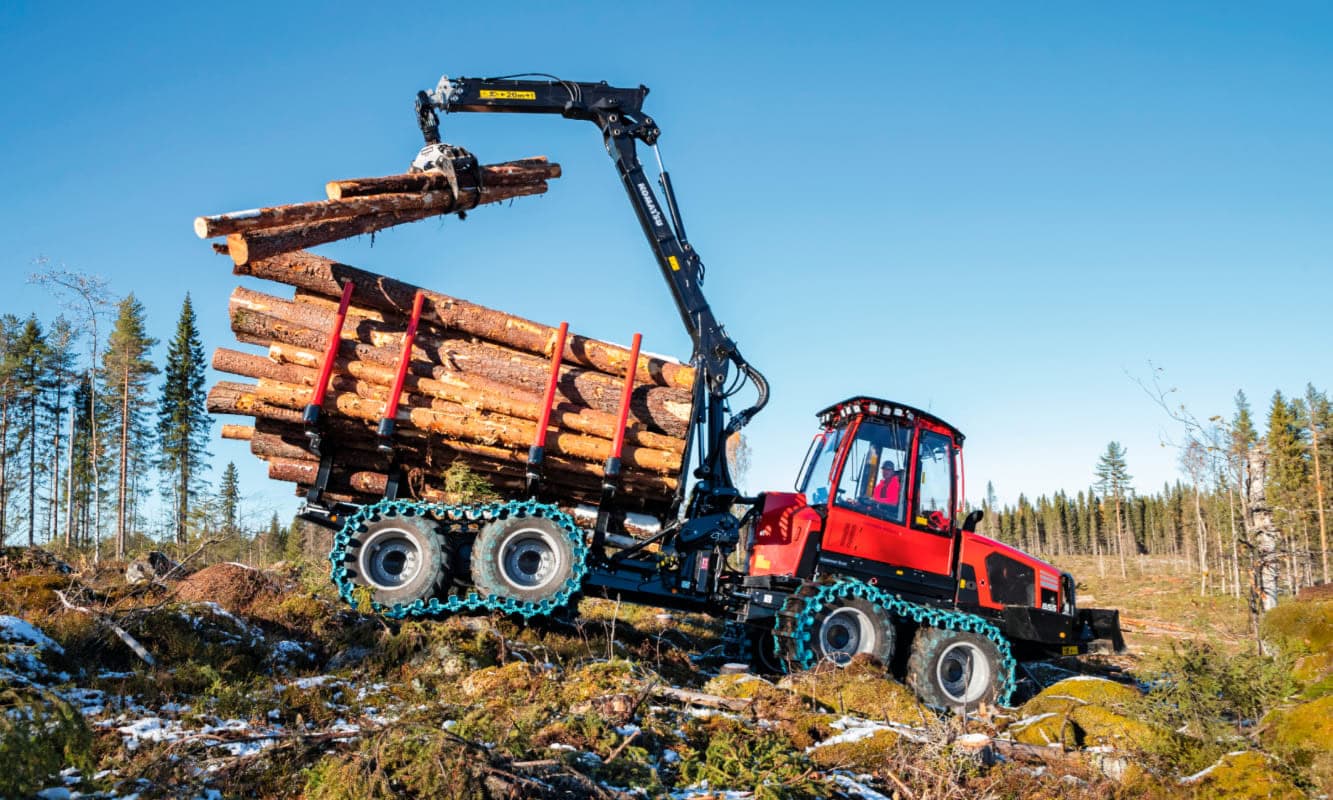
Forestry Machinery - Forwarder
Drives loader arm and log grapple.
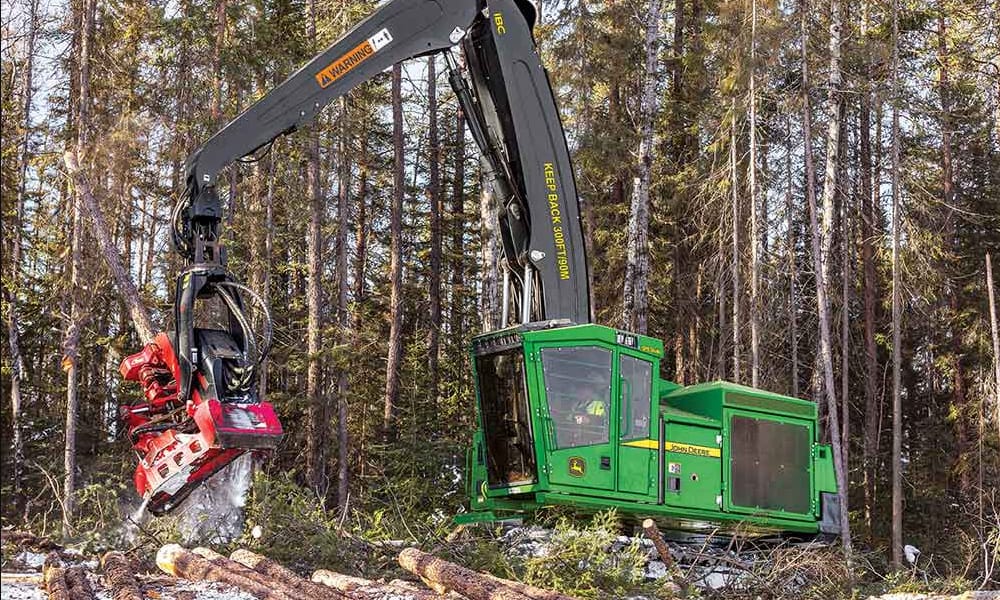
Forestry Machinery - Harvester
Controls grabbing and cutting head operation.
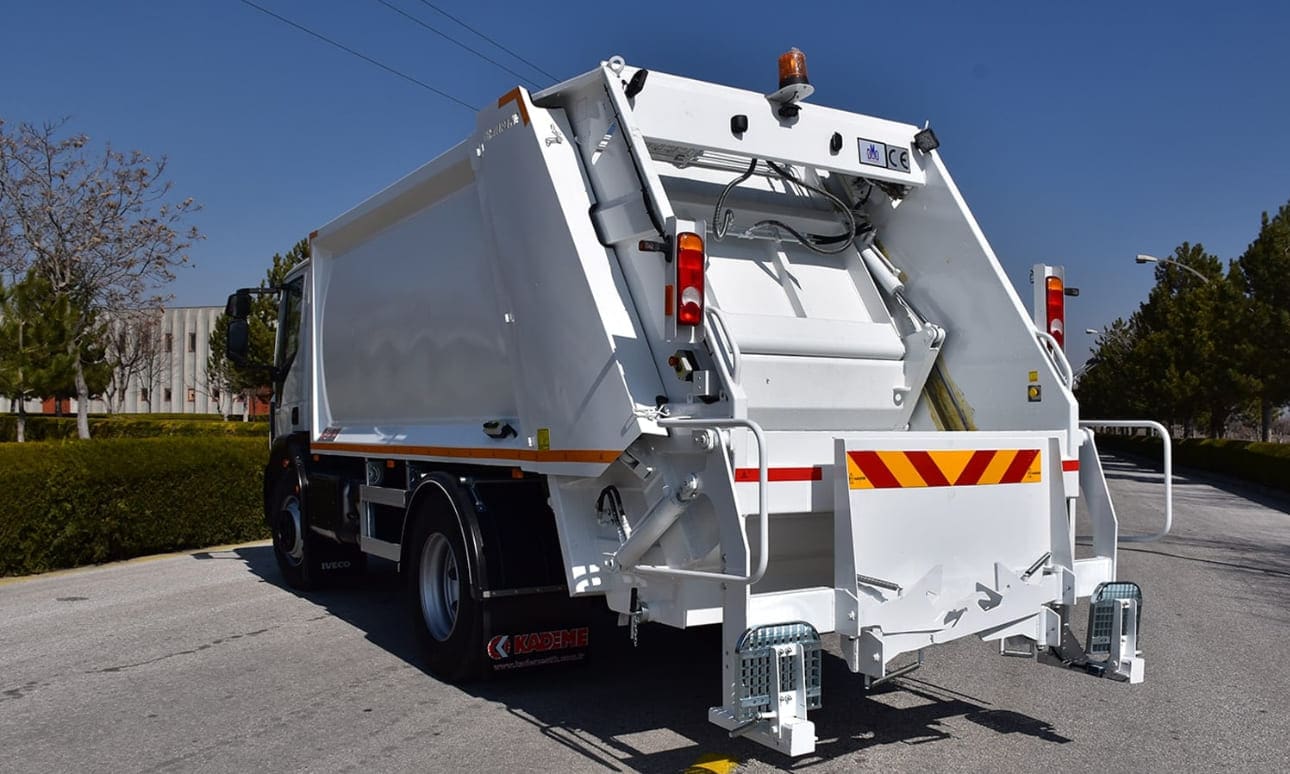
Municipal & Sanitation Equipment - Garbage Compactor
Compression mechanism power.
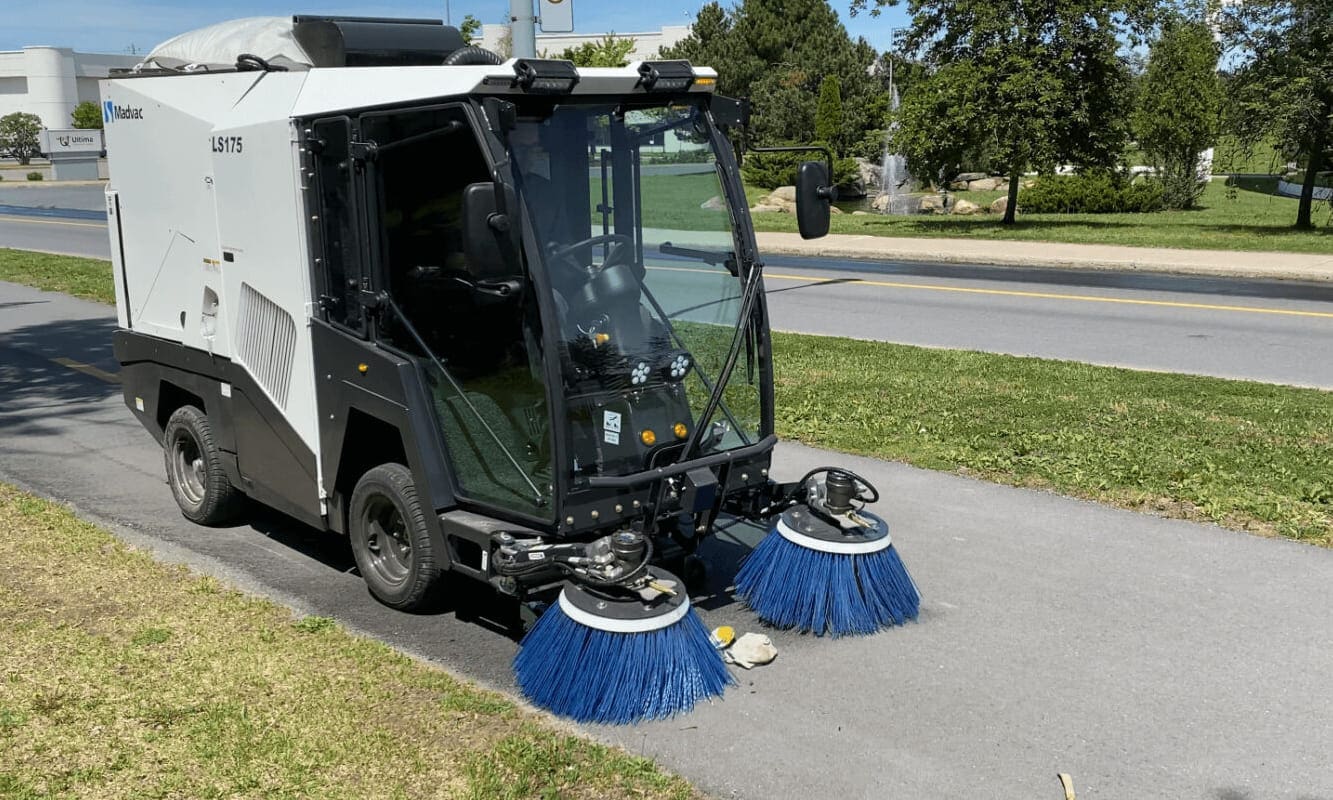
Municipal & Sanitation Equipment - Street Sweeper
Drive brush rotation and vacuum system.
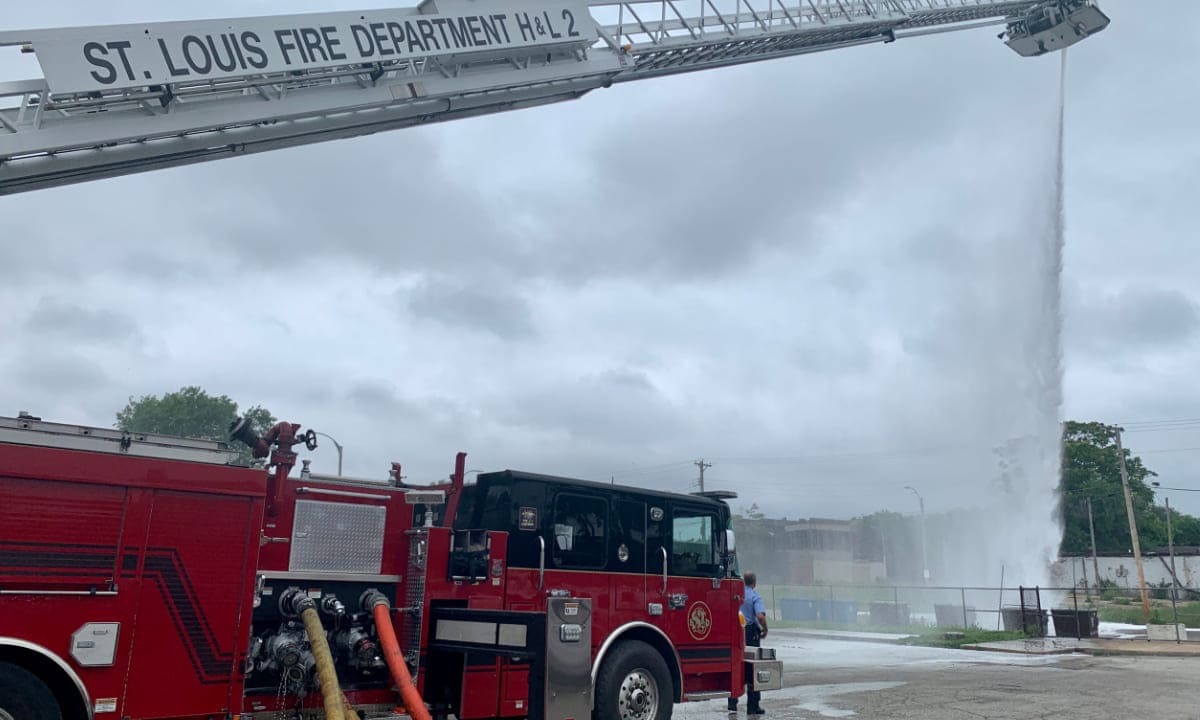
Special Vehicler - Fire Truck
Drive ladder extension and water pump.
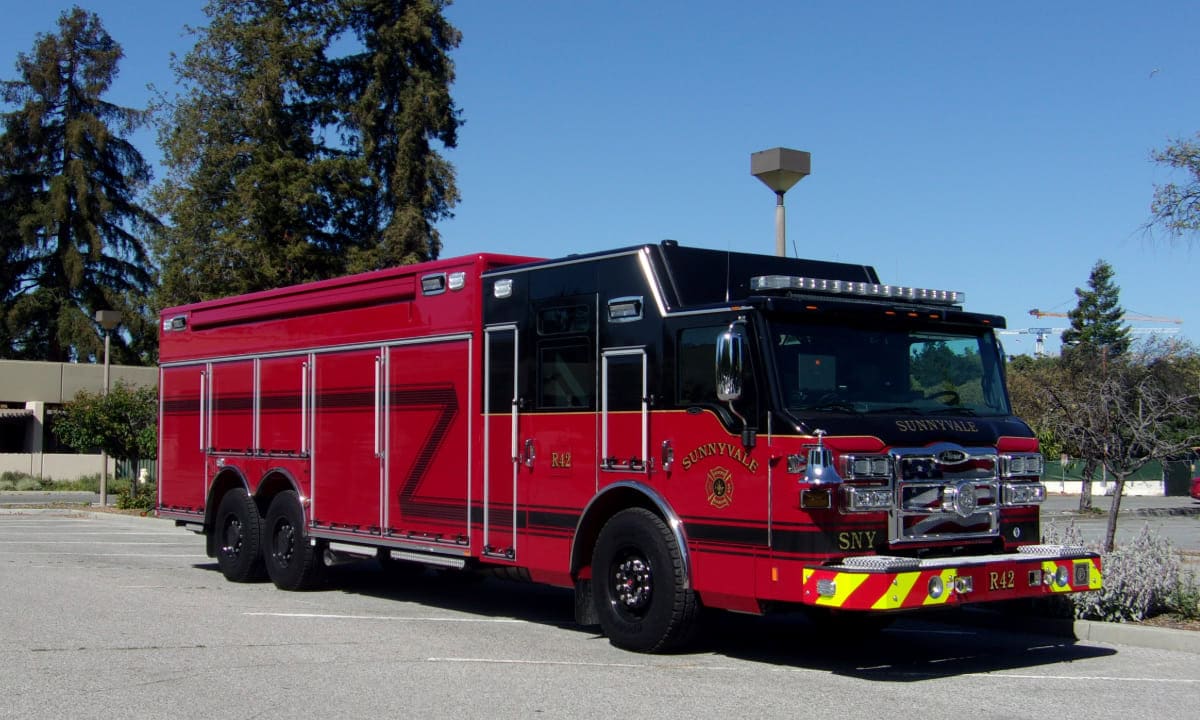
Special Vehicler - Rescue Vehicle
Support hydraulic rescue tools like cutter.
Tips On How To Maintain And Extend Service Life Of Medium-pressure Hydraulic Gear Pump
Proper maintenance of 16-25 MPa medium-pressure hydraulic gear pumps is critical to extend service life, maintain stable pressure output, and reduce downtime in diverse industrial applications such as construction, agriculture, material handling, and manufacturing. Below are essential maintenance practices backed by industry data and best practices:
1. Regular Inspections and Condition Monitoring
Frequency: Perform visual and operational inspections every 500 operating hours or quarterly, whichever comes first.
What to Check: Examine gear wear, shaft seals, bearing condition, and pump housing for cracks or corrosion. Early detection of wear can prevent catastrophic failures.
Data Insight: Studies show that pumps with regular condition monitoring reduce unexpected breakdowns by up to 40%, significantly lowering maintenance costs.
2. Proper Break-In (Running-In) Procedure
Initial Operation: After installation or overhaul, run the pump at 50-70% of rated speed and pressure for 2-4 hours to allow gear teeth and internal surfaces to properly mate.
Purpose: This process minimizes initial wear and improves volumetric efficiency by up to 10%, enhancing pump longevity and system stability.
3. Maintain Clean Hydraulic Fluid and Filtration
Fluid Quality: Use hydraulic oil with ISO cleanliness level of 18/16/13 or better to prevent abrasive wear.
Filter Maintenance: Replace or clean filters every 1000 operating hours or as recommended by the manufacturer.
Impact: Contaminated fluid is the leading cause of gear pump failure, responsible for over 60% of premature wear cases.
4. Monitor Operating Parameters and Avoid Overpressure
Pressure Limits: Ensure system pressure stays within the 16-25 MPa rating to avoid excessive mechanical stress.
Temperature Control: Keep operating temperature between 40°C and 80°C; temperatures above 90°C accelerate seal degradation and reduce pump life by up to 30%.
Vibration and Noise: Unusual vibration or noise can indicate misalignment or cavitation; immediate troubleshooting can prevent costly damage.
5. Scheduled Preventive Maintenance
Routine Checks: Every 2000 hours, conduct a full pump inspection including gear backlash, shaft runout, and internal clearances.
Component Replacement: Replace seals, bearings, and worn gears proactively based on inspection results to avoid unplanned downtime.
ROI: Preventive maintenance can extend pump life by 25-40% and improve overall hydraulic system uptime.
FAQs
Widely used in construction machinery (excavators, loaders), agricultural machinery (tractors, combine harvesters), material handling equipment (forklifts, port cranes), etc., to meet medium pressure and high reliability demand scenarios.
It is necessary to comprehensively evaluate the working pressure (16-25 MPa), flow demand (L/min), medium type (mineral oil or bio-based hydraulic oil), installation space and environment (temperature resistance, dustproof level). It is recommended to provide specific parameters to consult the supplier.
Check the seal wear every 500-1000 hours, and replace the hydraulic oil filter regularly to avoid contamination; long-term shutdown requires emptying the medium and rust prevention. It is recommended to shorten the maintenance cycle under high load conditions.
In the range of 16-25 MPa, gear pumps are lower in cost, compact in structure and resistant to pollution, but their efficiency is slightly lower than that of plunger pumps. Suitable for medium-pressure scenarios with limited budget or space.
Optimized internal leakage design reduces energy consumption, is compatible with biodegradable hydraulic oil, complies with ISO 15380 environmental protection standards, and is suitable for green manufacturing and sustainable development needs.
Loud noise: Check cavitation or bearing wear in the suction line; Pressure fluctuation: Clean or replace clogged filters and confirm that the oil viscosity meets the requirements.
Support customized flange interfaces, shaft extension types (ISO/SAE standards), corrosion-resistant materials (such as nickel-plated gears), and provide OEM/ODM services to meet specific mechanical integration needs.
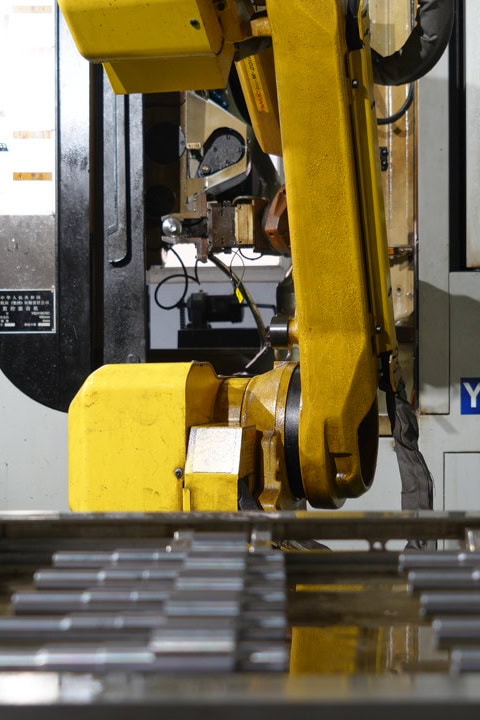
Enpower Your Machine Business Now!
Welcome to consult installation, maintenance and care, after-sales, price and other issues, we will reply you as soon as possible.
Support customization and distributor.