Above 25 MPa Hydraulic Gear Pump: Efficient and Durable Industrial Power Solutions
Fairy Deer Benefits Of Above 25 MPa High-pressure Hydraulic Gear Pump
High Operating Pressure: Rated pressure ≥ 25 MPa with maximum surge pressure up to 30 MPa, suitable for demanding work conditions;
Durable Construction: Aluminum housing with cast iron end plates enhances wear resistance and pump lifespan;
Varied Flow Rates: Available from 7.56 GPM to over 30 GPM to meet diverse equipment requirements;
Compact Design: Small footprint with easy installation, compatible with standard SAE ports;
Eco-Friendly Manufacturing: Lead-free materials and plating-free process comply with modern environmental standards;
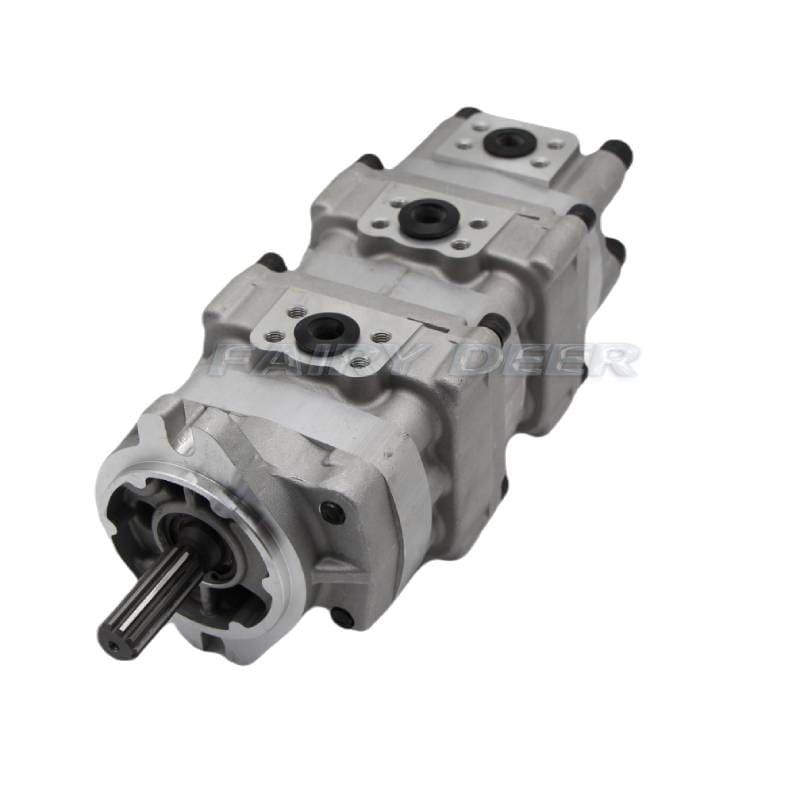
COMPARISON
Pressure Ratings and Applications:
High-pressure hydraulic gear pumps are engineered for pressures above 25 MPa, ideal for heavy-duty industrial machinery and demanding hydraulic systems. Medium-pressure pumps operate between 16-25 MPa, suited for general industrial equipment and moderate load applications.
Structural Design and Performance Advantages:
High-pressure pumps feature a rectangular five-piece modular design, compact and easy to machine, with low noise levels meeting top standards. Their volumetric efficiency reaches up to 95%, maintaining over 85% efficiency even at low speeds (125 RPM), making them ideal for variable frequency drive (VFD) energy-saving applications. Medium-pressure pumps have simpler structures with typical efficiencies between 50%-80%, and less optimal low-speed and energy-saving performance.
Materials and Durability:
High-pressure pumps use special alloy materials for internal rotating parts, offering strong impurity resistance and wear durability, extending lifespan and reducing maintenance. Medium-pressure pumps use more standard materials suitable for lower pressure and load conditions.
Energy Efficiency and Environmental Benefits:
High-pressure pumps support constant pressure operation at low speeds and VFD control, significantly reducing energy consumption with up to 50% power savings, meeting modern industrial energy-saving and environmental standards. Medium-pressure pumps have limited energy-saving capabilities.
Operating Pressure and Applications:
High-pressure hydraulic gear pumps are designed for pressures above 25 MPa, ideal for heavy-duty industrial machinery, construction equipment, hydraulic lifts, and high-intensity hydraulic systems, providing stable power under demanding conditions. Low-pressure gear pumps operate below 16 MPa, typically used in light machinery, lubrication, and low-pressure hydraulic transmission, with limited pressure capacity.
Structural Design and Performance Advantages:
High-pressure pumps feature an advanced rectangular five-piece modular design that is compact, with fewer parts, low noise, and volumetric efficiency up to 95%. They maintain over 85% efficiency even at low speeds (125 RPM), ideal for energy-saving variable frequency drives. Their design minimizes end-face leakage and radial unbalanced forces, extending pump life. Low-pressure pumps have simpler structures, lower cost, small size, and good self-priming, but suffer from high flow and pressure pulsations, higher noise, lower volumetric efficiency, and are unsuitable for heavy or prolonged high-pressure use.
Material Durability and Maintenance:
High-pressure pumps use high-strength alloy materials and precise manufacturing, offering excellent wear resistance and impurity tolerance, reducing failure rates and extending maintenance intervals. Low-pressure pumps use more standard materials and manufacturing, suitable for low-intensity use with more frequent maintenance.
Energy Efficiency, Environmental and Economic Benefits:
High-pressure pumps support low-speed constant pressure and variable frequency control, achieving significant energy savings up to 50%, meeting modern green manufacturing standards and helping reduce operational costs. Low-pressure pumps have limited energy-saving capabilities and cannot meet high-efficiency demands.
Spur gear pumps feature straight-cut gears with teeth perpendicular to the shaft axis. Their simple design makes them cost-effective and easy to maintain, widely used in applications handling low to medium viscosity fluids. They tolerate particulates well and provide reliable flow in less demanding environments. However, spur gear pumps tend to generate higher noise and vibration levels during operation, and their fluid flow pulsations can affect system smoothness and component lifespan.
In contrast, helical gear pumps have angled teeth that engage more gradually and smoothly, significantly reducing noise and vibration. The increased tooth contact area distributes load more evenly, enabling stable flow at higher pressures and speeds with improved volumetric efficiency. Helical pumps also offer better sealing performance, minimizing leakage and extending service life. Their drawbacks include higher manufacturing costs, more complex structures, and relatively greater maintenance requirements.
From the perspective of selection, helical gear pumps are preferable where noise reduction, vibration control, and high-pressure stable operation are critical. Spur gear pumps offer a cost-effective solution when budget constraints exist and noise or pulsation tolerance is acceptable. Both types are fixed displacement pumps suitable for consistent flow demands in hydraulic systems, but helical pumps provide superior performance and user experience.
Recommended High-pressure Gear Pump
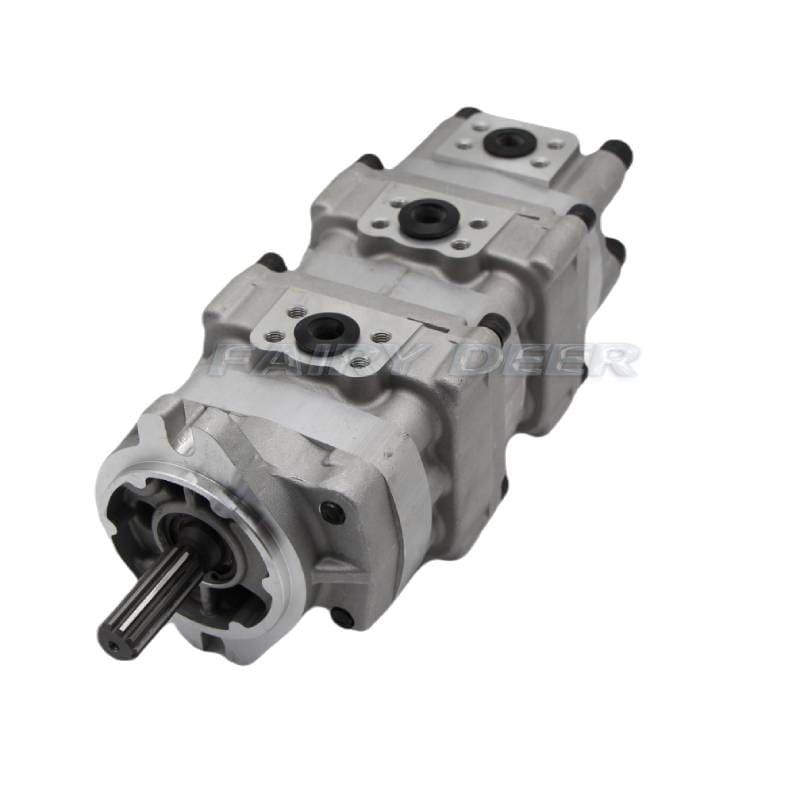
Single Gear Pump For KOMATSU PC75UU-2 Excavator
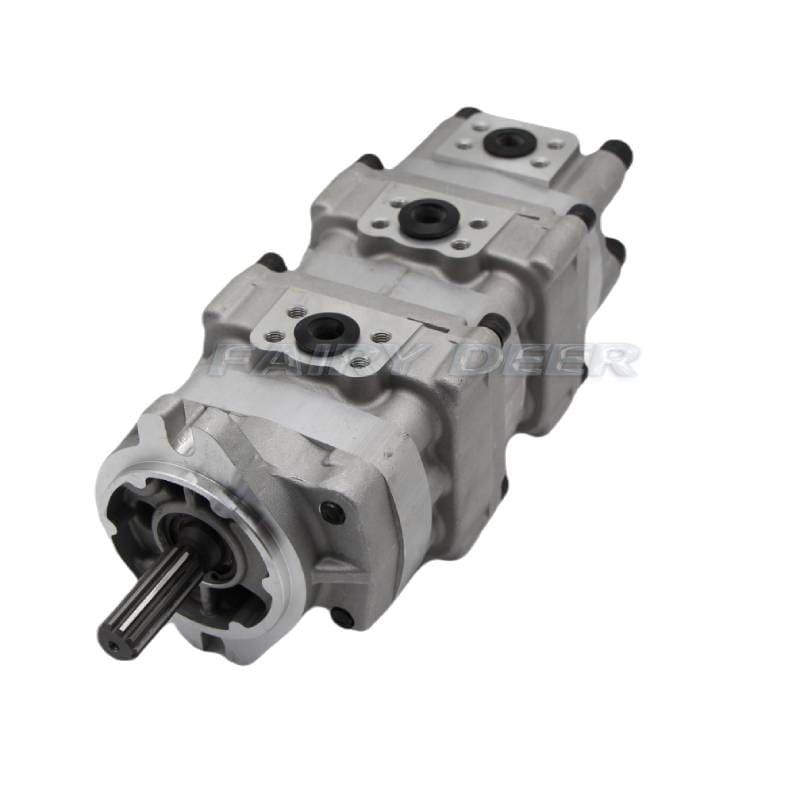
Double Gear Pump For CATERPILLAR E305.5 E306 E308 Excavator
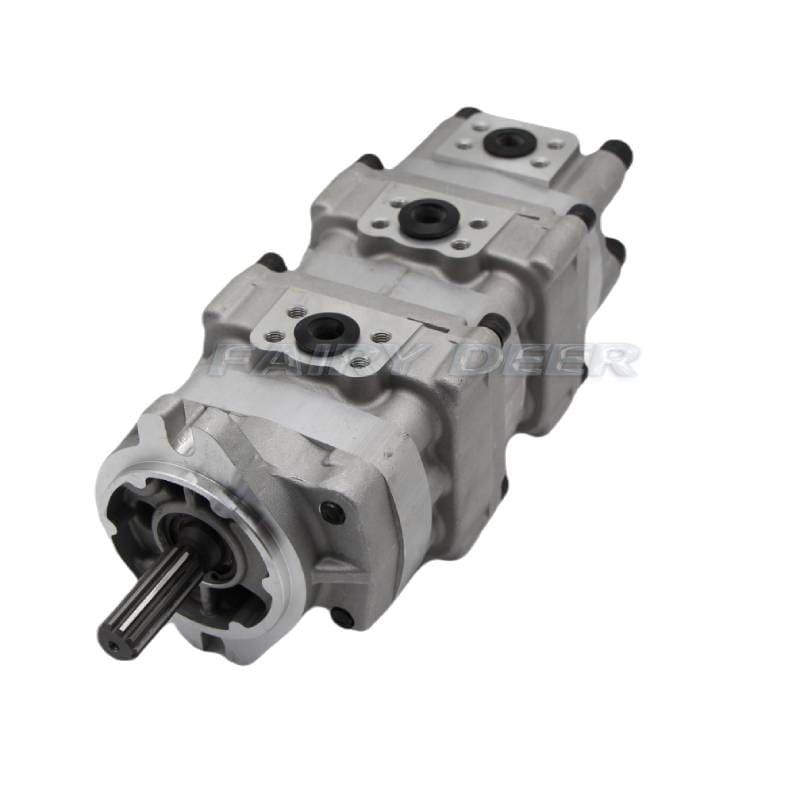
Triple Gear Pump For KOMATSU 3-5 Ton Excavator
High-Pressure Hydraulic Gear Pumps: Efficient and Reliable Power Solutions for Diverse Industries
Discover our high-pressure hydraulic gear pumps rated above 25 MPa, engineered for construction machinery, manufacturing equipment, agricultural machines, and environmental systems. Experience energy-efficient, durable, and stable power delivery that keeps your industrial operations running smoothly.
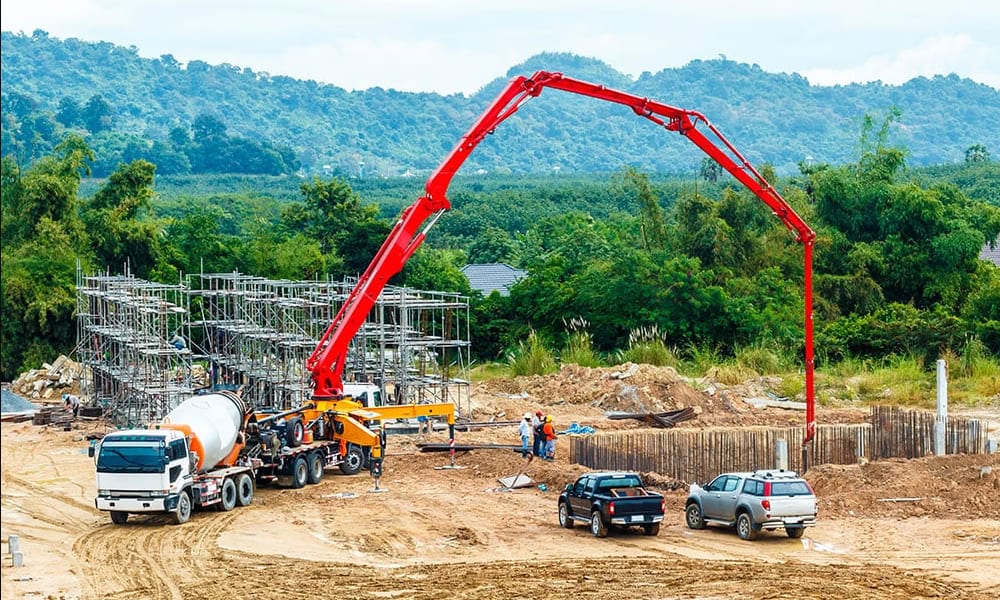
Construction Machinery - Concrete Pump Truck
Transport high-pressure concrete slurry.
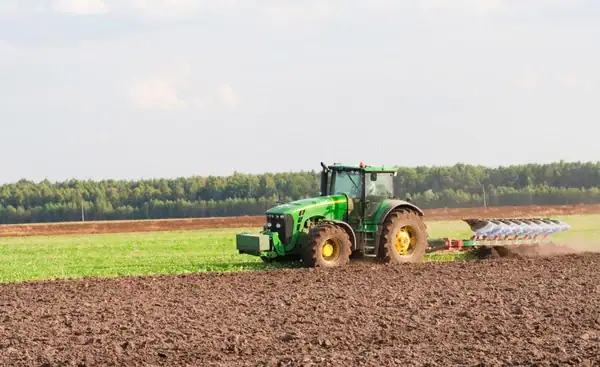
Agricultural Machinery - Tractor Hydraulic System
Drive tillage equipment, suspension devices and steering systems.
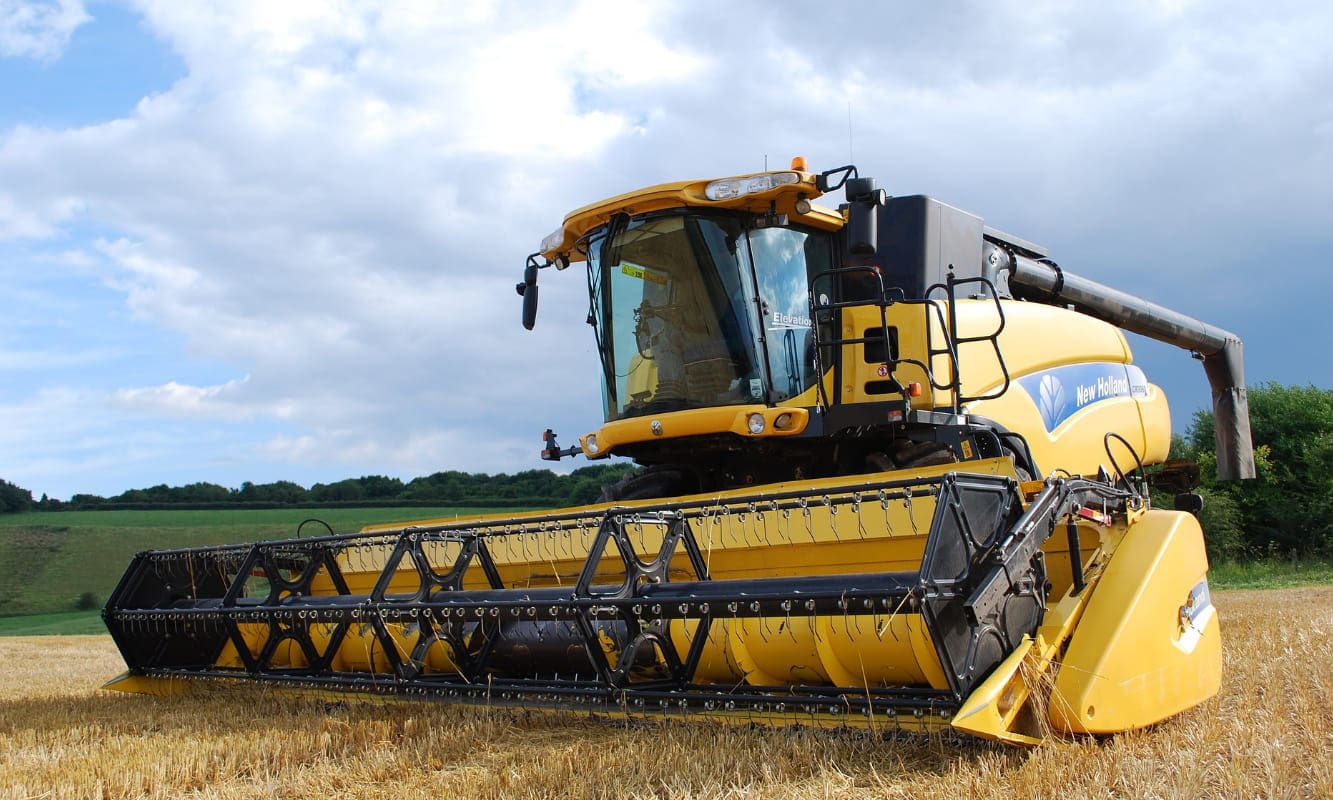
Agricultural Machinery - Combine Harvester
Control hydraulic power of cutters and conveyors.
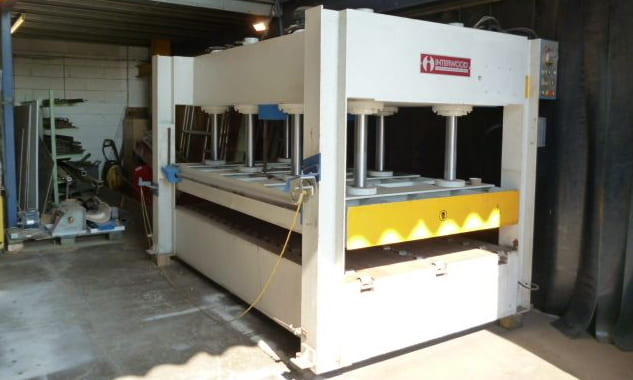
Industrial Manufacturing Equipment - Press Machine
Such as hydraulic power units of metal molding machines, with pressures up to 25 MPa.
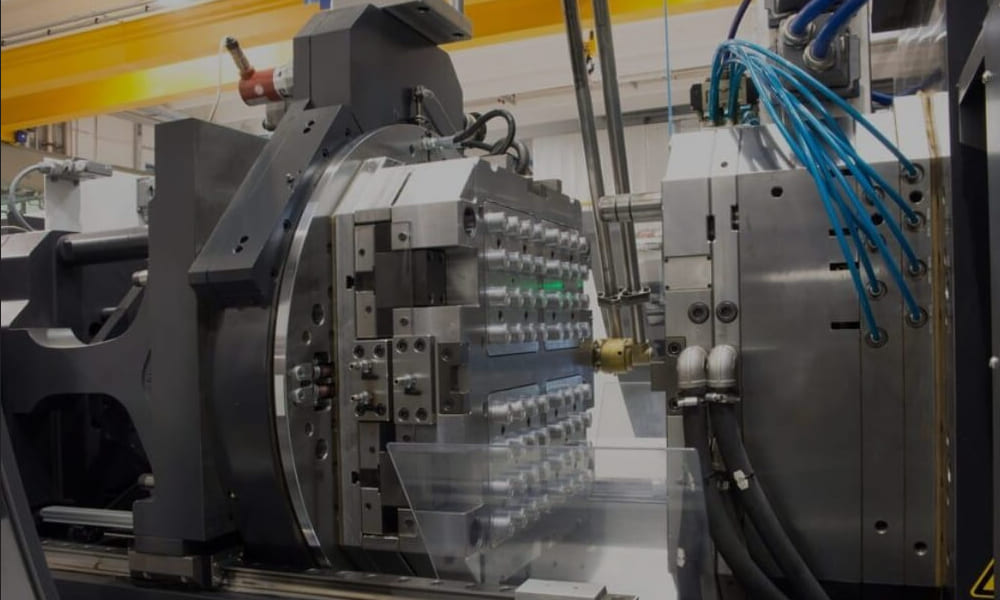
Industrial Manufacturing Equipment - Injection Molding Machine
High-precision control of injection pressure of molten plastic.
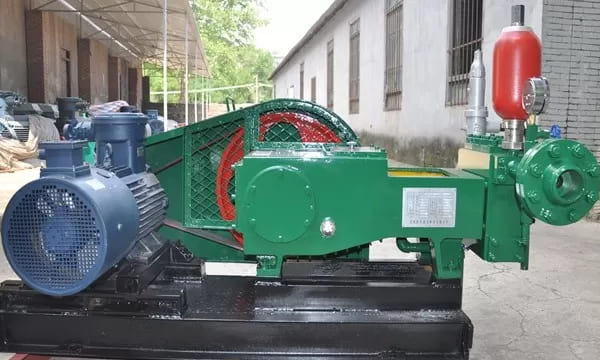
Petrochemical Industry - Residual Oil Transfer Pump
Transporting low-quality fuel at high temperature (300°C) and high pressure (above 4.0 MPa).
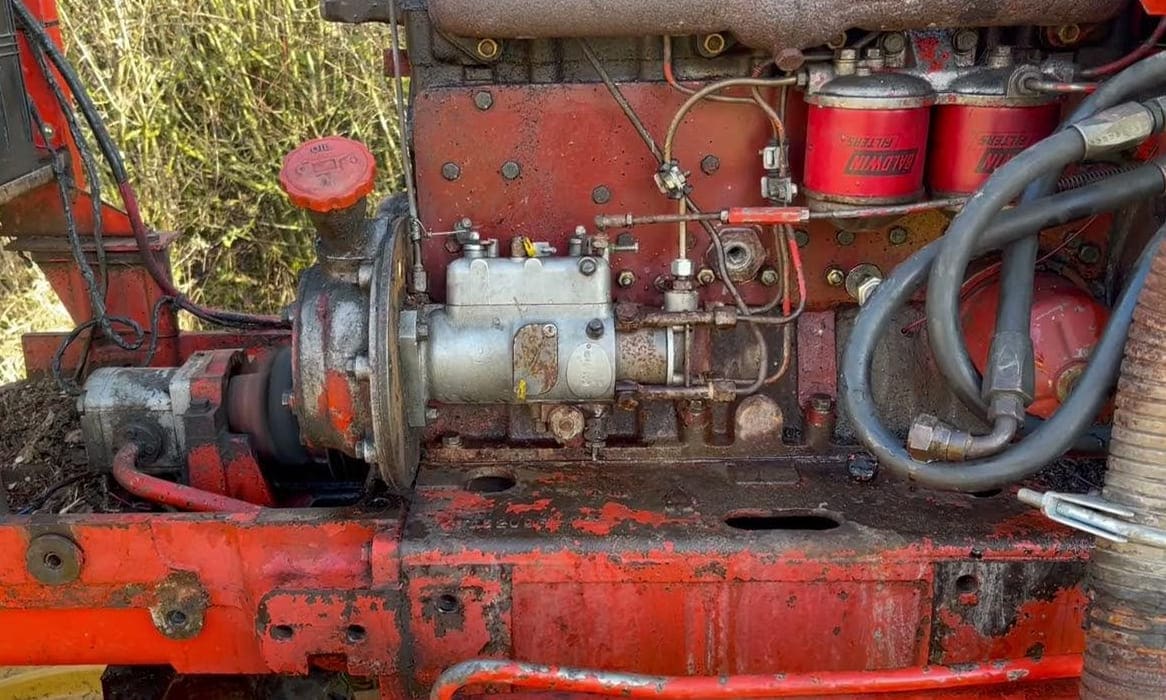
Petrochemical Industry - High-Pressure Injection System
Used for precise metering of catalysts or additives in refineries.
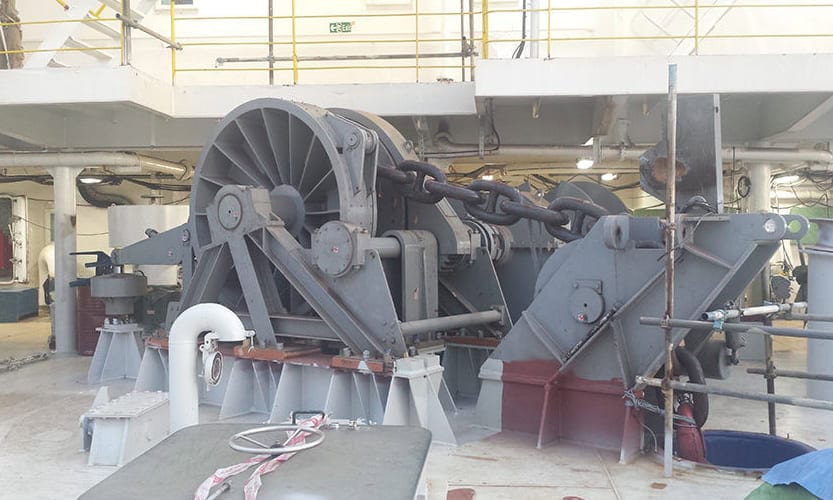
Marine and Offshore Engineering - Deck Machinery
Hydraulic drive for anchor winches and winches.
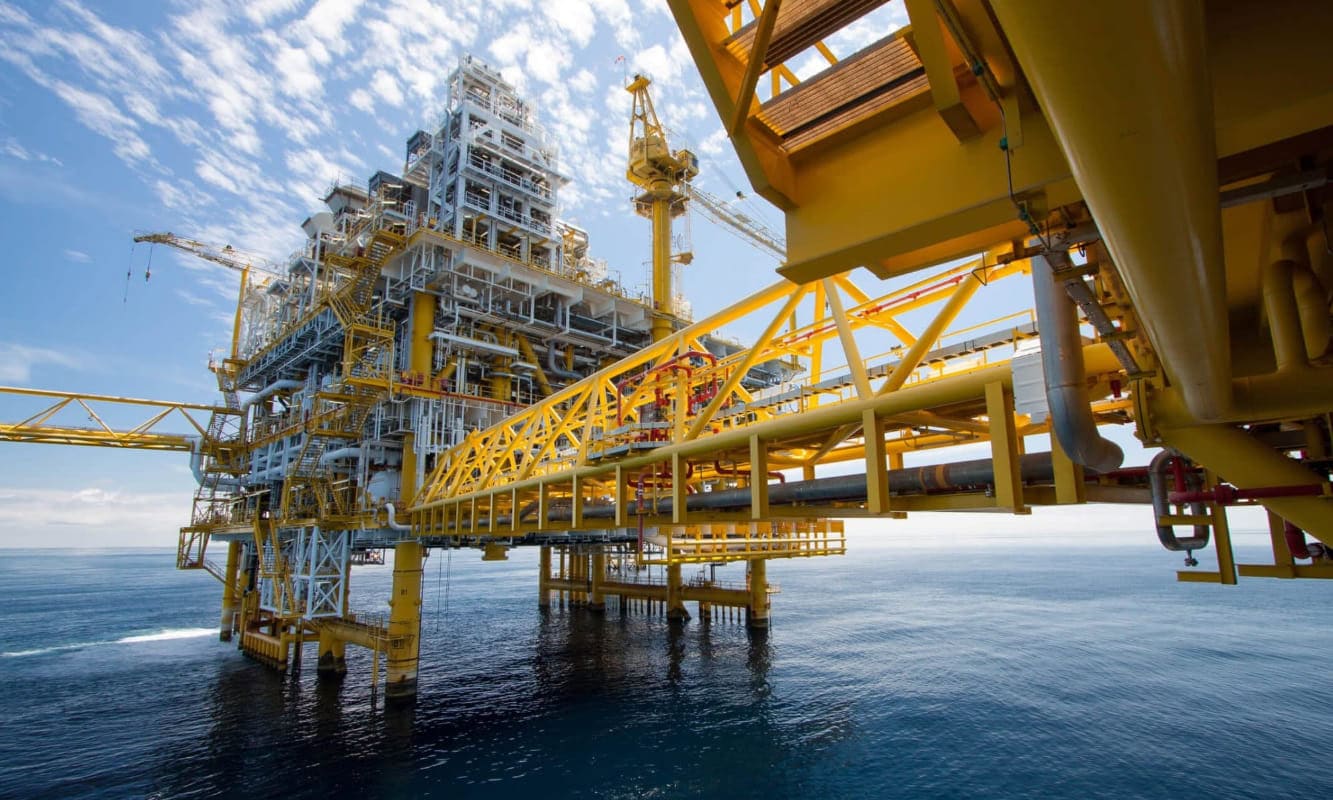
Marine and Offshore Engineering - Offshore Platform Hydraulic
Pressure control for drilling equipment.
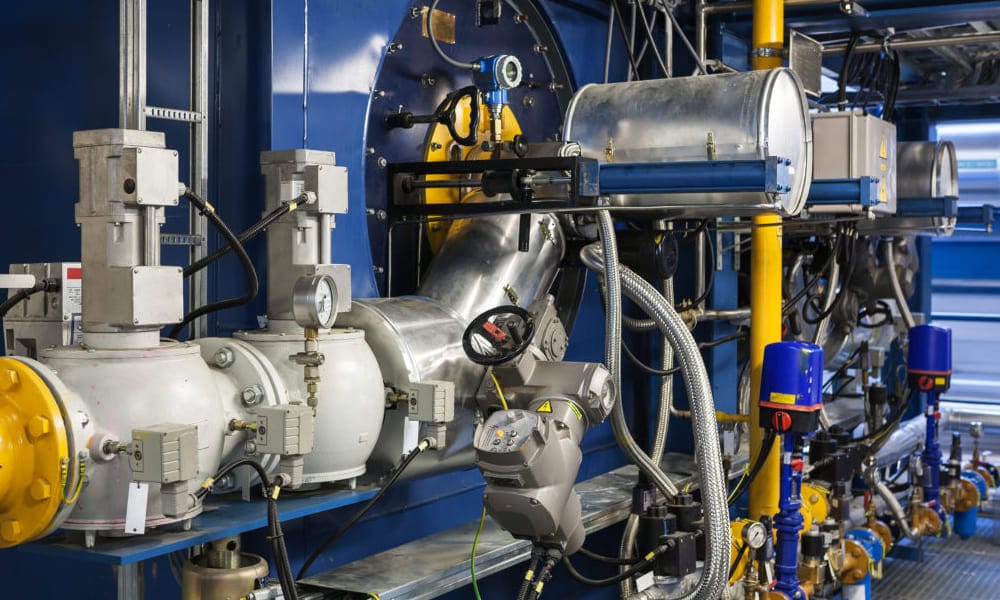
Energy Sector - Fuel Boiler Feed System
High-pressure transportation of heavy oil or biofuels.
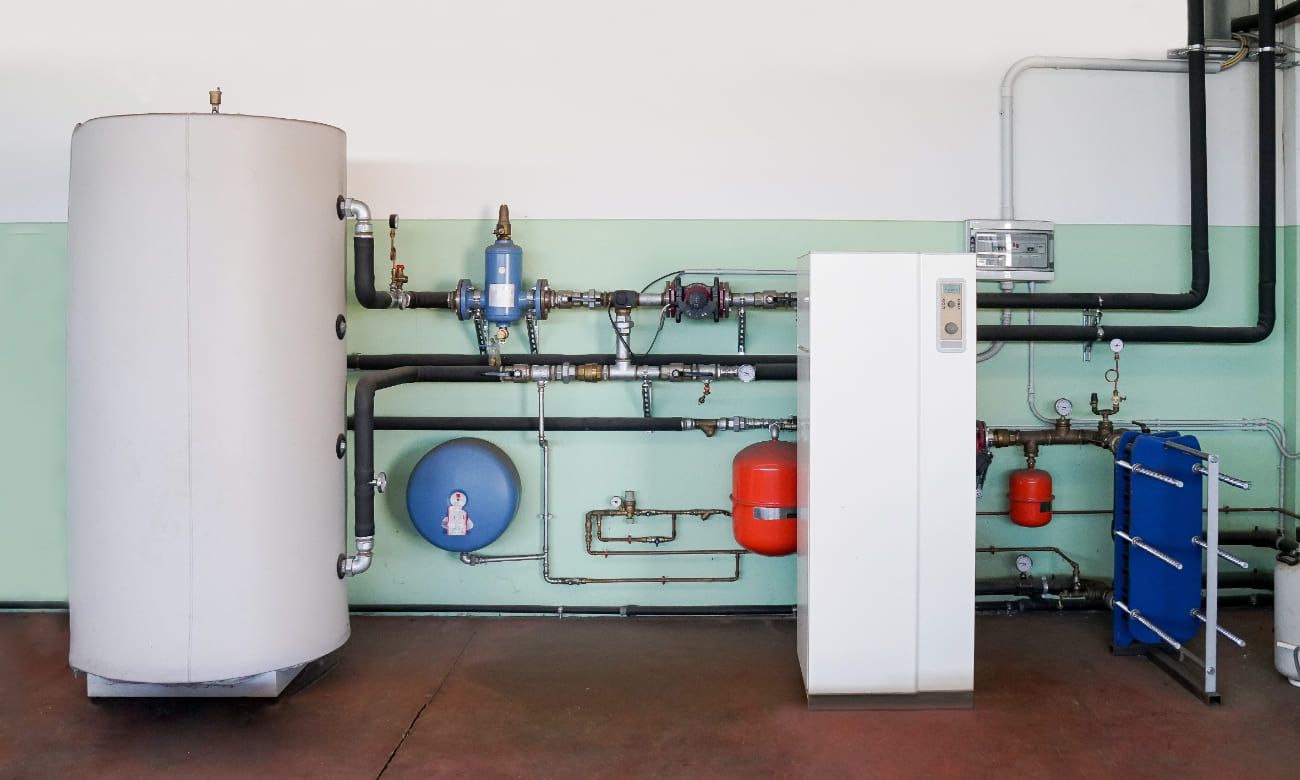
Energy Sector - Geothermal Pump
High-temperature and high-pressure fluid circulation system.
Tips On How To Maintain And Extend Service Life Of High-pressure Hydraulic Gear Pump
Proper maintenance of high-pressure hydraulic gear pumps is essential to maximize their service life and ensure optimal performance across various industries such as construction, manufacturing, agriculture, and environmental systems. Here are key maintenance tips to help customers maintain efficient and reliable hydraulic systems:
1. Regular Inspections
Periodically inspect the pump for signs of wear, leakage, abnormal noise, or vibration. Check seals, shafts, and mounting bolts to ensure everything is tight and intact. Early detection of issues prevents costly downtime and repairs.
2. Proper Lubrication and Hydraulic Fluid Monitoring
Use high-quality hydraulic fluids compatible with high-pressure gear pumps. Regularly monitor fluid levels and quality, replacing contaminated or degraded fluids promptly to prevent internal wear and corrosion.
3. Controlled Operating Conditions
Avoid operating the pump beyond its rated pressure (>25 MPa) and speed limits. Implement proper system filtration to reduce contamination and maintain stable temperature to prevent overheating, ensuring long-term reliable operation.
4. Scheduled Bedding-in and Calibration
For new or rebuilt pumps, perform a controlled bedding-in process by gradually ramping up pressure and flow to stabilize internal clearances and improve volumetric efficiency. Periodically calibrate system parameters to maintain optimal performance.
5. Clean System Components
Keep hydraulic lines, filters, and reservoirs clean to avoid contamination. Regularly replace filters and flush the system as needed. Clean components reduce wear and improve pump lifespan and energy efficiency.
FAQs
It is necessary to comprehensively consider the working pressure, flow rate, medium viscosity, temperature range and material compatibility (such as carbon steel/stainless steel). For example: Corrosion-resistant coated gears are required to transport high-temperature (>150°C) fuel. It is recommended to provide working condition parameters and let engineers customize the selection plan.
Use floating side plate design (such as patent CN102146915A) or two-way compensation seal technology to reduce end face gap leakage. Regularly replace high-pressure seals (such as fluororubber/Viton®).
General recommendations: check seals and bearings every 500 hours and replace hydraulic oil every 2000 hours. If the medium contains particles (such as mining machinery), it needs to be shortened to 300 hours and a filtration system needs to be installed.
Yes. For high-viscosity media (such as asphalt), a heating jacket is required; for corrosive liquids (such as acid), all stainless steel (SS316) or Hastelloy is recommended.
Optimize volumetric efficiency (>90%) and drive motor matching, and use variable frequency control (VFD) to adjust flow on demand. For example: energy consumption of injection molding machine is reduced by 15-20% in energy-saving mode.
Possible causes:
Cavitation → Check whether the inlet pipeline is blocked or the oil level is insufficient.
Gear wear → Disassemble and check the tooth surface and measure the clearance.
Oil contamination → Replace the filter element and test the ISO cleanliness level (target ≤18/16/13).
Mainstream manufacturers have passed ISO 4400 hydraulic standards, ATEX explosion-proof certification (petrochemical industry) and CE/PED certification. Some models support API 674 standards (petrochemical industry).
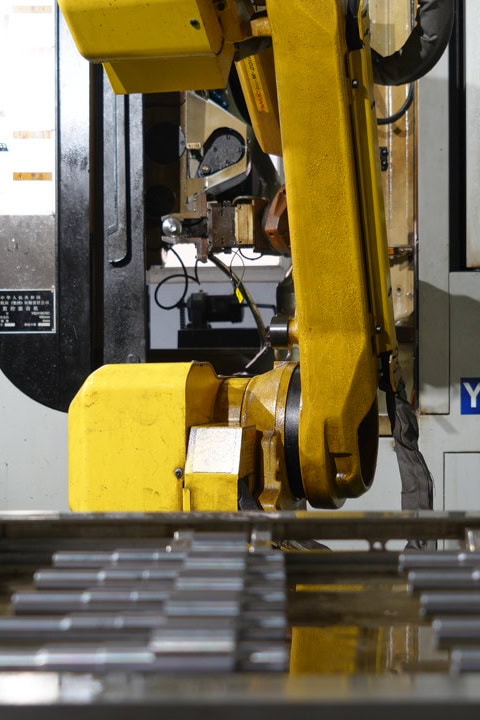
Enpower Your Machine Business Now!
Welcome to consult installation, maintenance and care, after-sales, price and other issues, we will reply you as soon as possible.
Support customization and distributor.