Core Materials and Formulas of Products
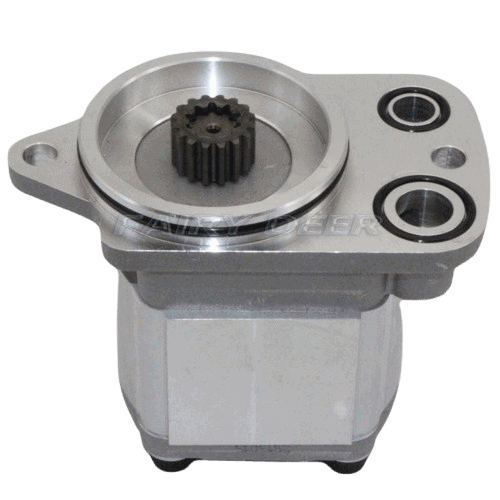
Key Parts Production Process
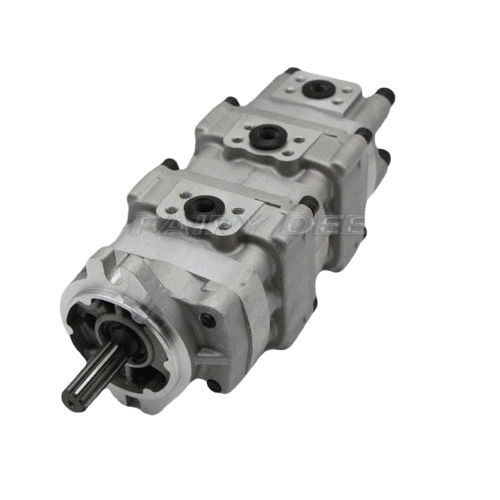
Assembly and Performance Optimization
Quality Testing and Certification
Our quality assurance combines comprehensive performance validation & authoritative certifications: 10-30MPa pressure-flow characteristic testing with multi-channel DAQ (1kHz sampling) maintains flow fluctuation ≤±1.5% (ISO 4400-2022 compliant). 500-hour accelerated endurance testing (80℃ oil + peak pressure shocks) achieves <2.8% efficiency decay, surpassing industry standards. Certified by TÜV Rheinland (EN ISO 13849-1 safety) and CE Machinery Directive, with SGS third-party reports (including HTHP test bench raw data), guaranteeing global compliance.
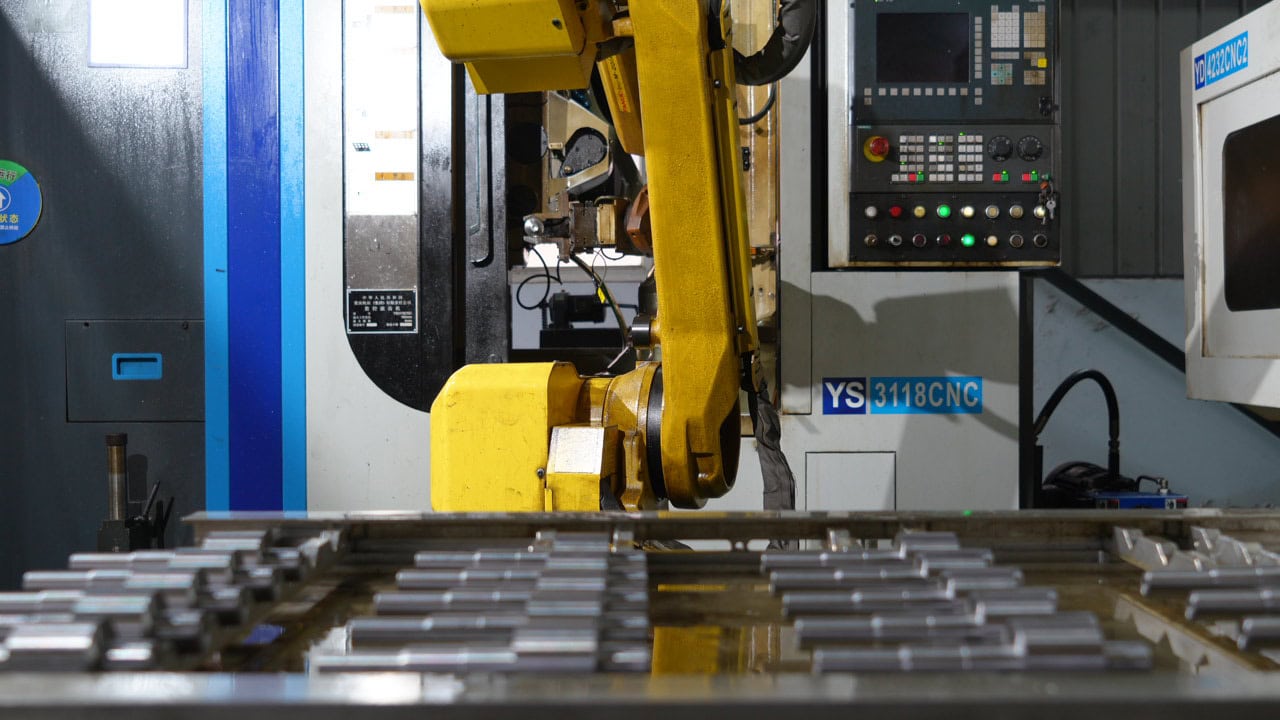
Product Advantages Comparison
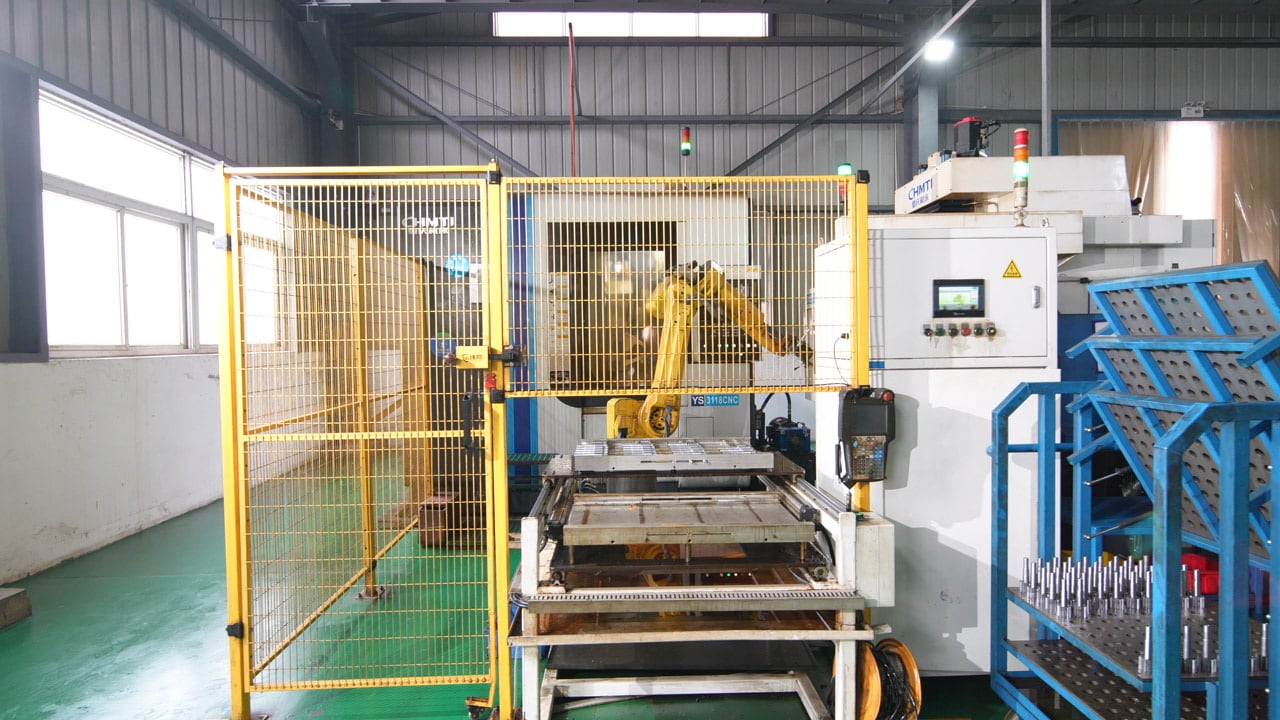
Provide Customized Design and Service
We deliver full-cycle hydraulic customization spanning 1-100cc/rev displacement (ISO 8423 ±0.5% tolerance), supporting flange/thread/clamp connections (EN 14471 compliant), with optional DLC coating (HV3000 hardness, 2000h salt spray resistance) or electroless nickel plating (50-80μm thickness, friction coefficient ≤0.08). Our modular digital platform (3D parametric modeling + CFD simulation) enables 48-hour rapid prototyping. Packaging solutions include EPE cushioning + IP67 cases with laser-engraved logos and RFID tags (storing pressure/flow/batch data), MOQ negotiable to 10 units for medical/construction applications.
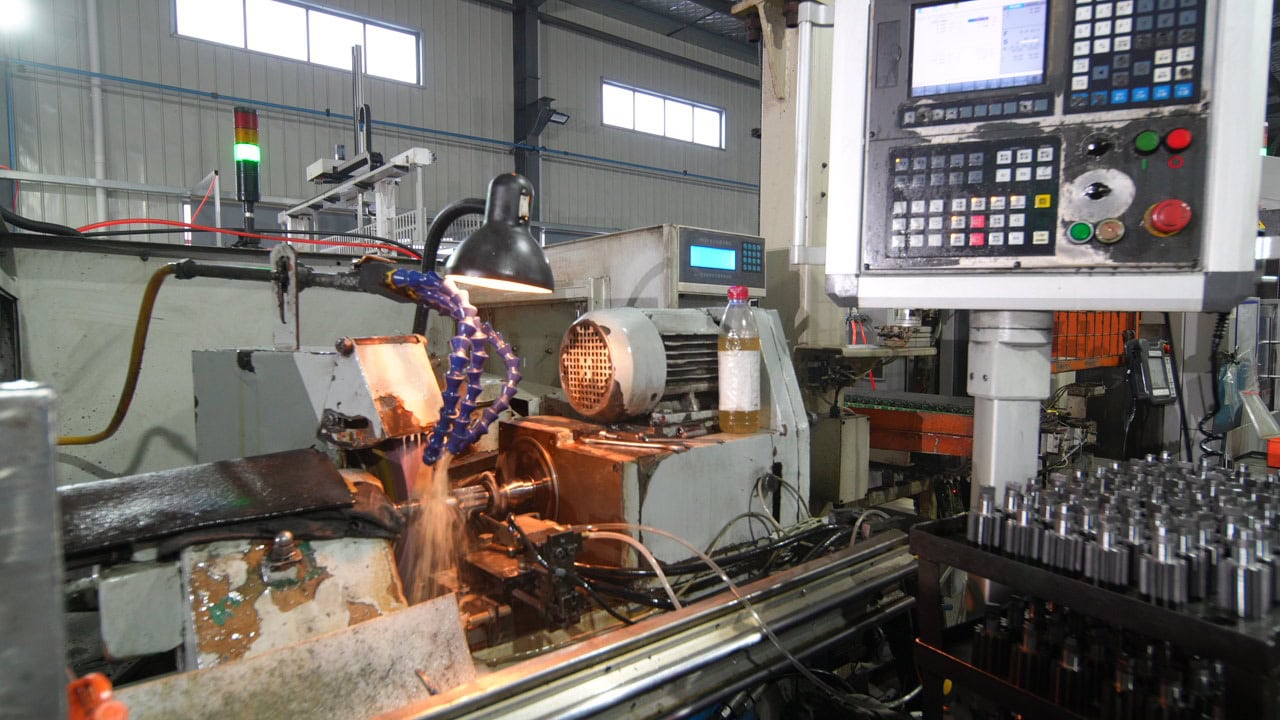