Internal Medium-Pressure 16-25 MPa Hydraulic Gear Pump - Efficient, Durable Hydraulic Solution
Fairy Deer Benefits Of Internal 16 - 25 MPa Medium-pressure Hydraulic Gear Pump
Low pulsation and smooth operation ensure minimal vibration and noise, enhancing system stability and operator comfort.
Robust aluminum construction provides lightweight durability and excellent heat dissipation.
Versatile mounting options with A-type elliptical flanges and keyed shafts for easy integration.
Rated for pressures up to 25 MPa, suitable for medium-pressure hydraulic circuits requiring consistent flow and pressure.
Ideal for engineering machinery, material handling, agricultural equipment, and industrial vehicles.
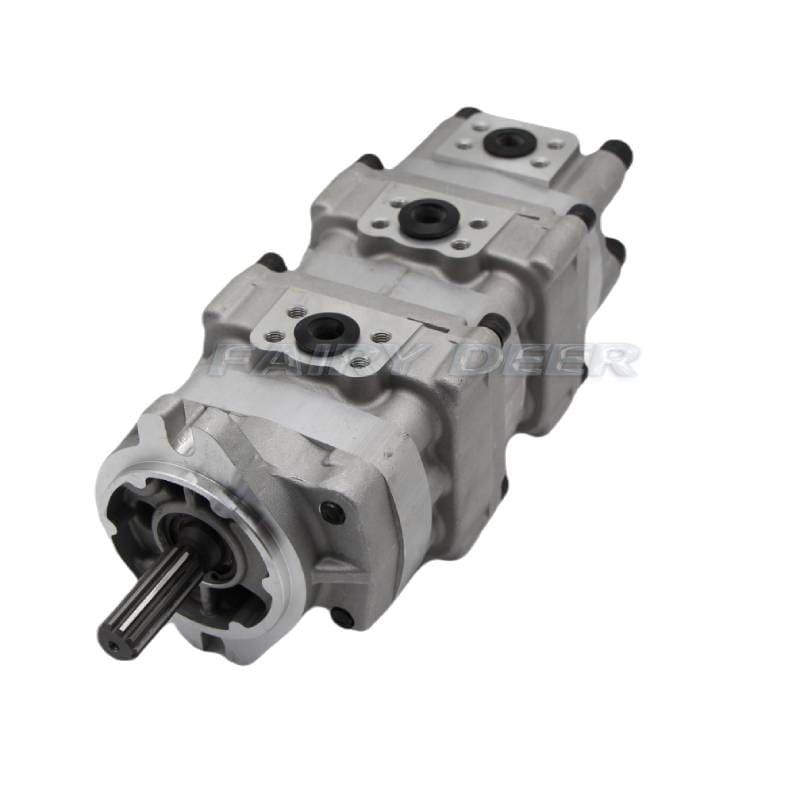
COMPARISON
Pressure Range and System Compatibility:
Internal gear pumps rated for 16-25 MPa are optimized for medium-pressure hydraulic systems commonly found in construction machinery, agricultural equipment, and material handling. Compared to high-pressure pumps (above 25 MPa), medium-pressure pumps provide stable pressure output suitable for most industrial hydraulic circuits, avoiding over-specification that leads to higher costs and maintenance burdens.
Compact Structure and Smooth Operation:
Medium-pressure internal gear pumps feature compact, lightweight designs with involute internal gear profiles, delivering smooth operation with minimal flow pulsation and low noise. High-pressure pumps generally require more robust, complex structures that can increase weight and noise. Thus, medium-pressure pumps offer superior vibration reduction and quieter working environments.
Efficiency and Energy Consumption:
Designed with axial and radial pressure compensation, medium-pressure pumps maintain high volumetric efficiency even at low speeds and viscosities, reducing energy consumption and heat generation. While high-pressure pumps handle greater loads, they may experience increased friction and leakage losses, making medium-pressure pumps more energy-efficient in typical applications.
Fluid Compatibility and Self-Priming:
Medium-pressure internal gear pumps handle a wide viscosity range (5–1500 cst) and exhibit strong self-priming capabilities, suitable for lubricants and similar fluids with varying thickness. High-pressure pumps often require cleaner, less viscous fluids due to their reinforced design, limiting versatility. Medium-pressure pumps thus adapt better to diverse operating conditions.
Maintenance and Service Life:
With simpler structures and less wear on components, medium-pressure pumps offer longer maintenance intervals and lower repair costs. High-pressure pumps endure higher mechanical stresses, potentially increasing maintenance frequency and expenses. For customers prioritizing cost-effectiveness and reliability, medium-pressure internal gear pumps present a more attractive option.
Pressure Capacity and Application Scope:
Internal gear pumps rated for 16-25 MPa are tailored for medium-pressure hydraulic systems, providing stable pressure and flow for demanding applications in construction machinery, agriculture, and material handling. Low-pressure pumps (below 16 MPa) suit light-duty or low-pressure systems but lack the capacity to handle higher loads and complex conditions, limiting their application and system performance.
Design and Operational Stability:
Medium-pressure internal gear pumps feature precision involute internal gears with compact structure, smooth operation, minimal flow pulsation, and low noise, greatly enhancing system stability and operator comfort. Low-pressure pumps, while simpler, may experience flow fluctuations and increased noise under moderate to heavy loads, affecting overall equipment performance.
Efficiency and Energy Consumption:
Medium-pressure pumps incorporate axial and radial pressure compensation, maintaining high volumetric efficiency even at low speeds and viscosities, reducing energy consumption and heat generation for better energy savings. Low-pressure pumps tend to lose efficiency under higher loads, resulting in increased energy use, which is less favorable for modern energy-efficient systems.
Fluid Compatibility and Self-Priming:
Medium-pressure internal gear pumps handle a wide viscosity range (5–1500 cst) and exhibit strong self-priming capabilities, suitable for diverse and challenging operating conditions. Low-pressure pumps have more limited fluid viscosity and self-priming capacity, restricting their versatility.
Service Life and Maintenance Costs:
Thanks to wear-resistant materials and optimized design, medium-pressure pumps have longer service life and extended maintenance intervals with lower costs, ideal for long-term stable operation. Low-pressure pumps may suffer accelerated wear under heavier loads, increasing maintenance frequency and expenses, impacting overall cost-effectiveness.
Compact Design & Reliability:
Internal gear pumps utilize asymmetric gear engagement (e.g., involute gears + crescent separator) with only 1 bushing in fluid contact, reducing wear points by 50% compared to external pumps requiring dual bearings. This design is ideal for abrasive fluids like waste oil or filled polymers.
Energy Efficiency:
With adjustable clearances (down to 0.001″) and volumetric efficiency ≥90%, internal pumps reduce energy consumption by 15-20% when handling high-viscosity fluids (e.g., 500cSt oil at 5.5kW vs. 6.8kW for external pumps).
Low Noise & Vibration:
Internal pumps operate at ≤70dB due to continuous fluid transfer, versus ≥80dB for external pumps. This makes them preferable for noise-sensitive environments like pharmaceutical cleanrooms.
Maintenance & Cost:
Internal pumps’ single-bushing design extends service intervals to 8,000-10,000 hours, lowering annual maintenance costs by 30-40% (e.g., from $12,000 to $7,500 in a refinery case).
Extreme Condition Adaptability:
Capable of handling fluids from -40°C to 800°C, internal pumps outperform external pumps (limited to ≤150°C) in applications like molten sulfur transfer or high-temperature asphalt processing.
Recommended Internal Medium-pressure Gear Pump
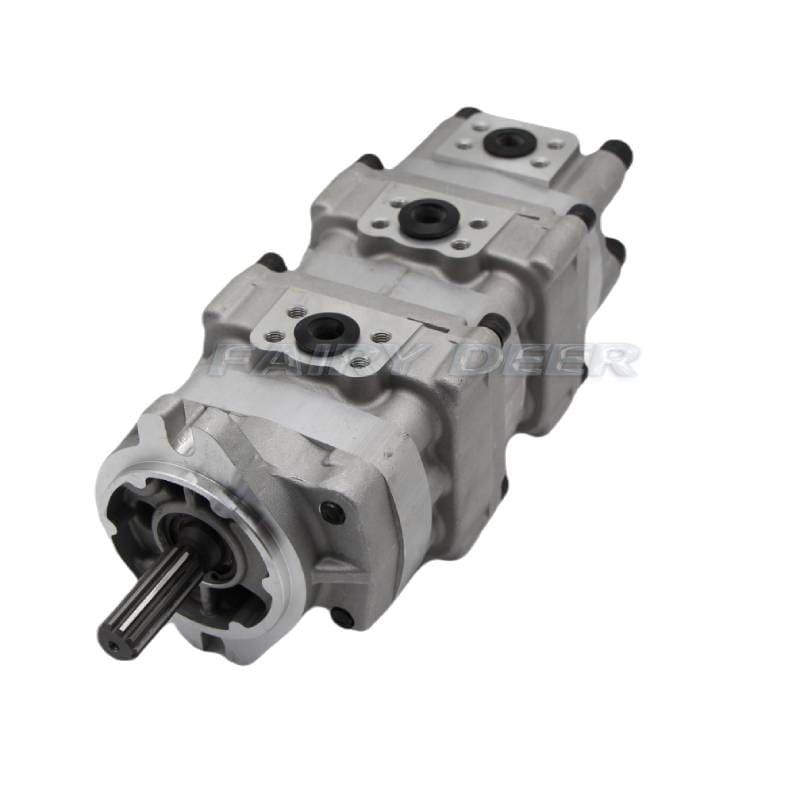
Single Gear Pump For KOMATSU PC75UU-2 Excavator
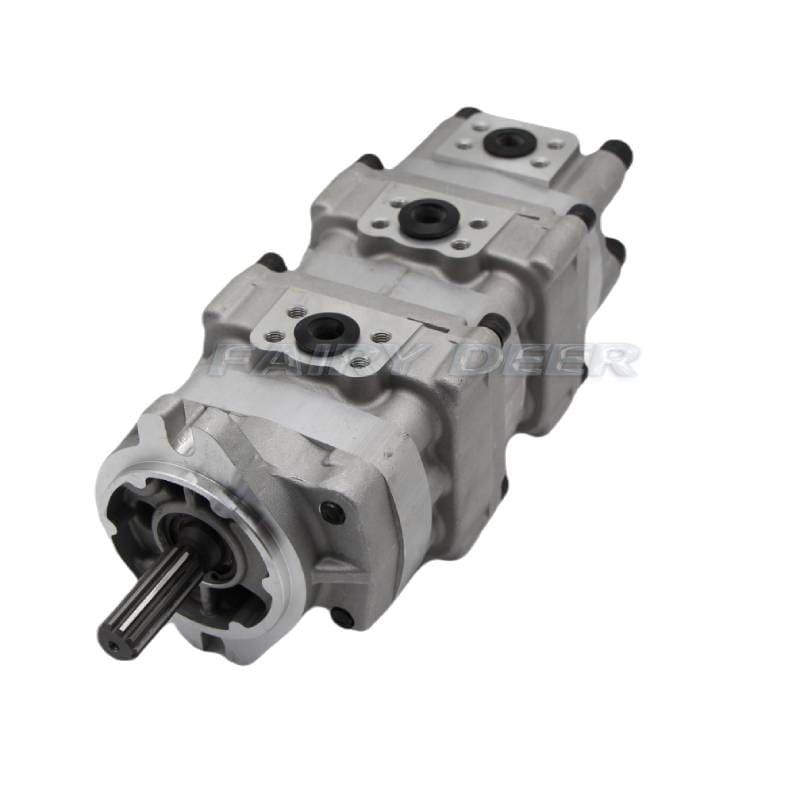
Double Gear Pump For CATERPILLAR E305.5 E306 E308 Excavator
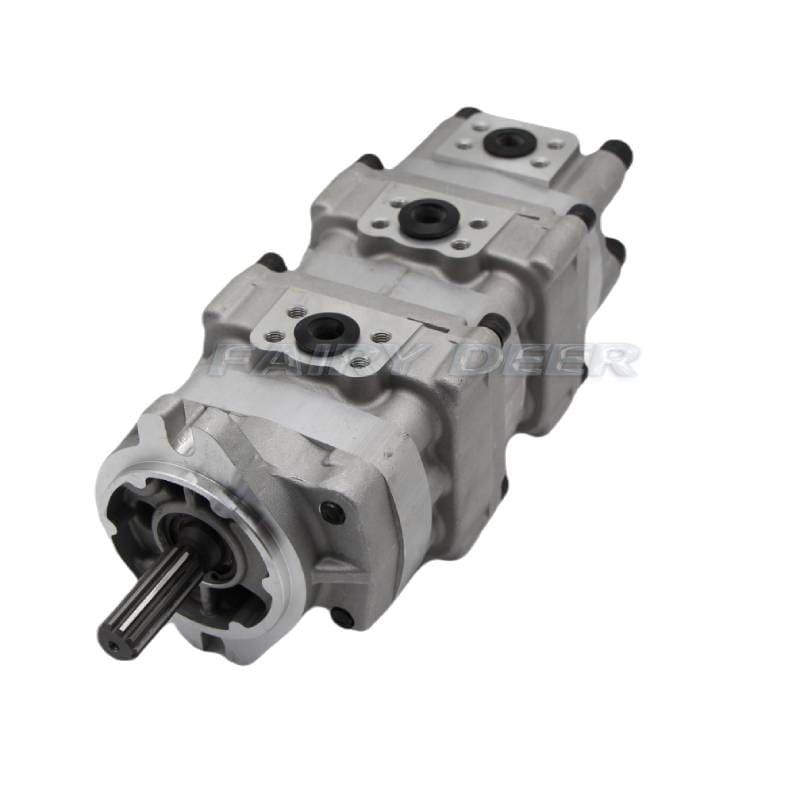
Triple Gear Pump For KOMATSU 3-5 Ton Excavator
Internal Medium-Pressure Hydraulic Gear Pumps: Built To Last In Demanding Environments
Explore internal medium-pressure hydraulic gear pumps, robustly constructed for reliable performance in harsh industrial settings. Operating between 16-25 MPa, these pumps offer exceptional durability, consistent pressure, and minimal maintenance. The optimal choice for heavy machinery, construction equipment, and tough applications.
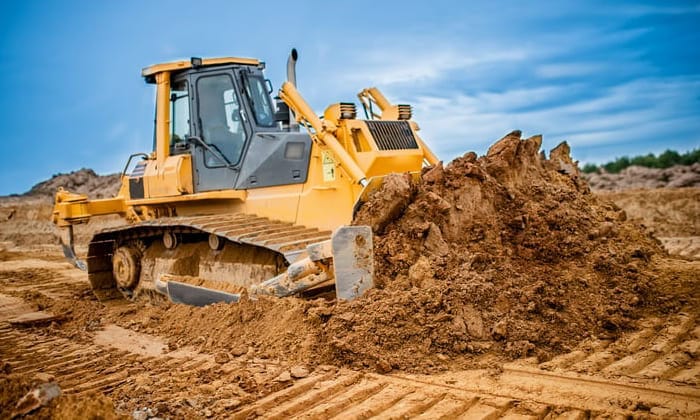
Construction Machinery - Bulldozer
Drive hydraulic system to control the power operation of excavating arm and bulldozer blade (such as digging, leveling).
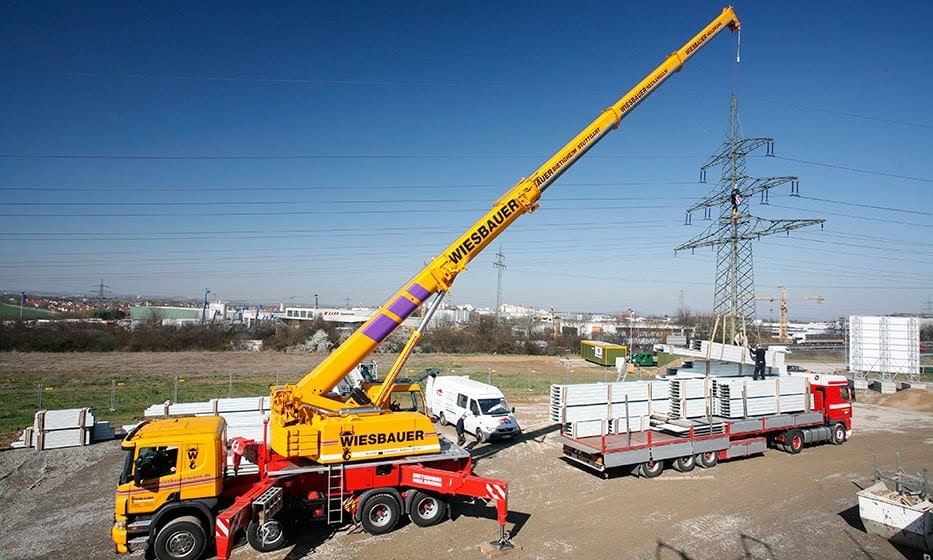
Construction Machinery - Crane
Provide high-pressure hydraulic power to drive boom extension and heavy lifting device.
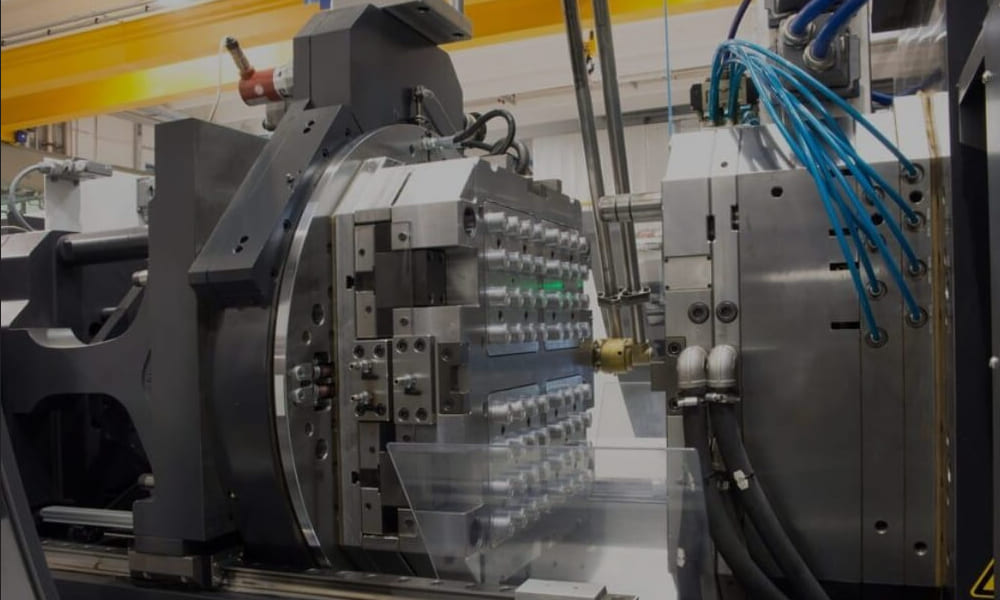
Industrial Equipment - Injection Molding Machine
Provide power for mold opening and closing, injection unit and ejection system.
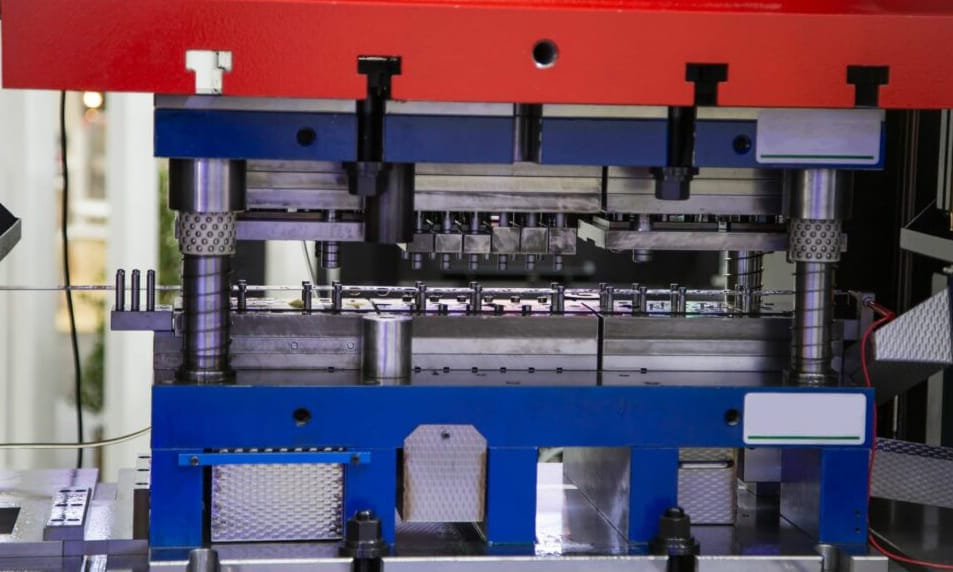
Industrial Equipment - Hydraulic Presse
Drive metal sheet forming, punching and stamping processes.
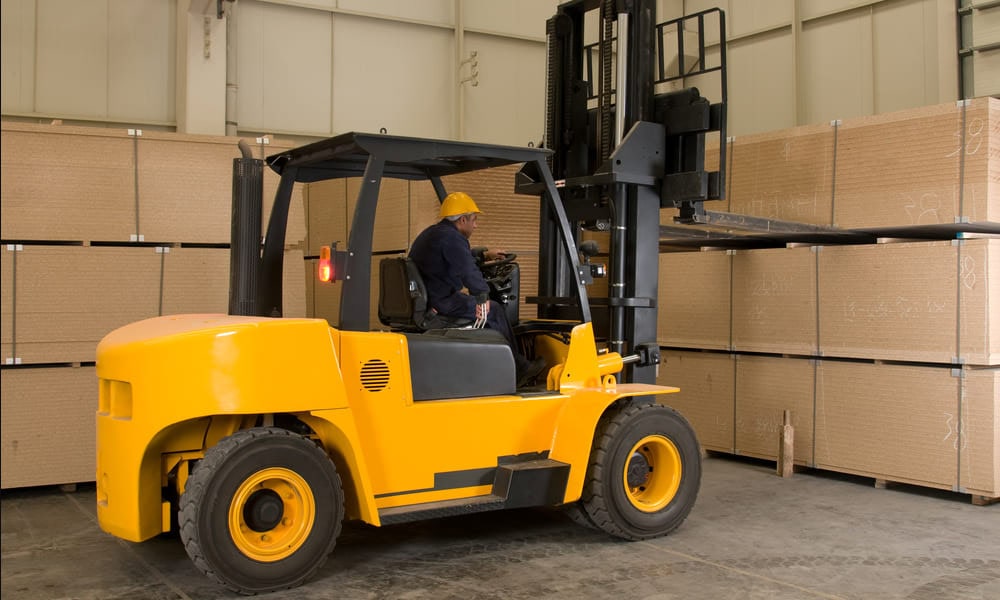
Logistics & Transportation - Forklift
Control the lifting and tilting of forks to achieve cargo loading and unloading.
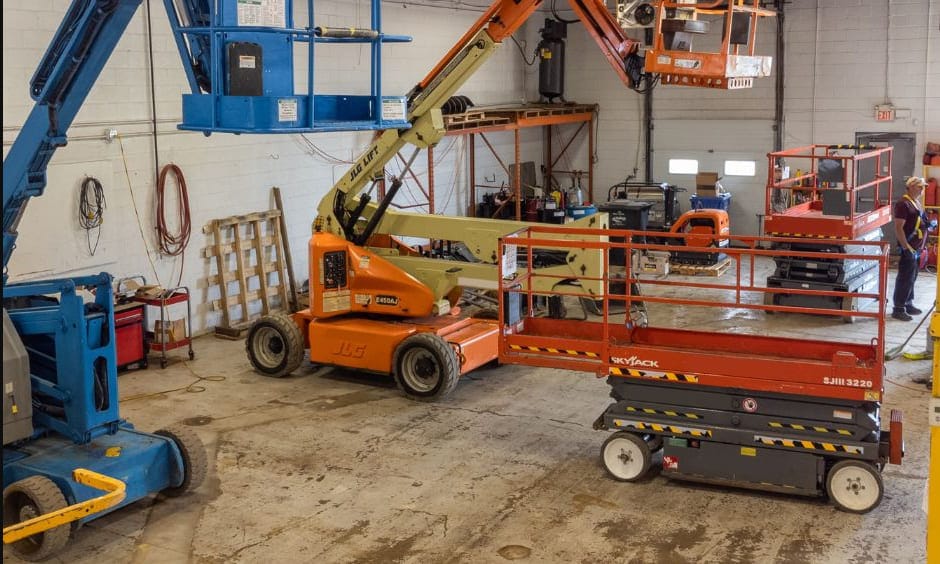
Logistics & Transportation - Scissor Lift
Adjust the height of the work platform for warehousing or high-altitude operations.
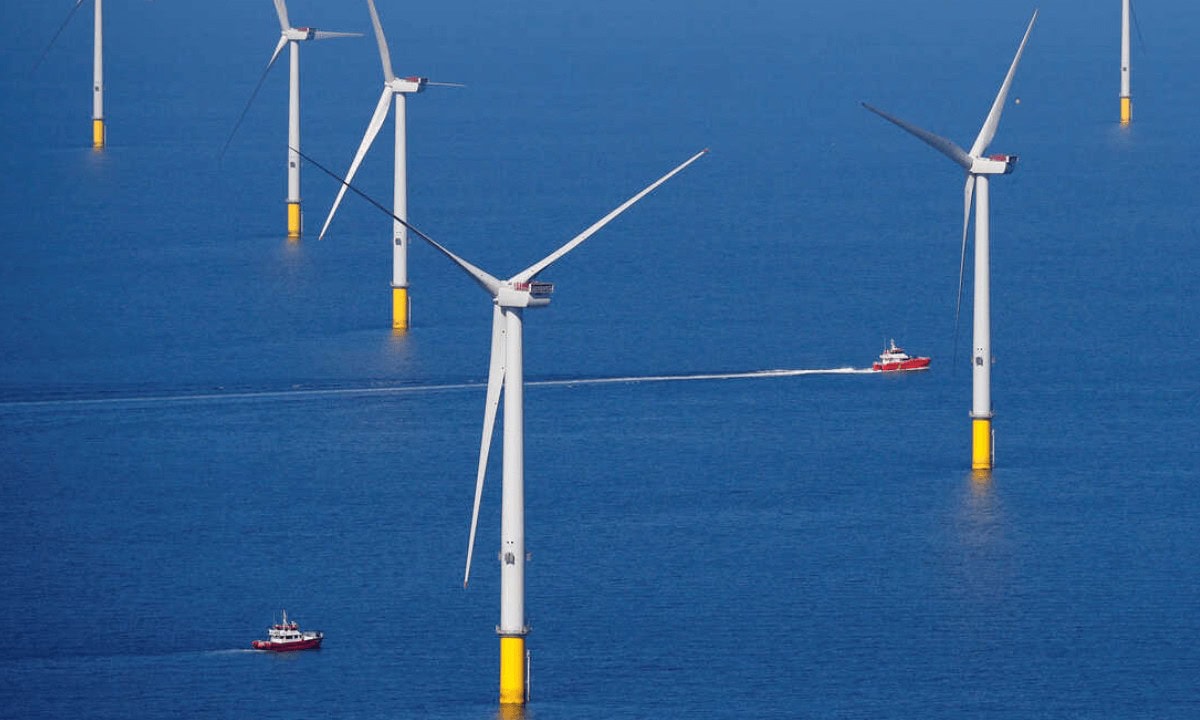
Energy Sector - Wind Turbine
Adjust the blade pitch system to optimize wind energy capture efficiency.
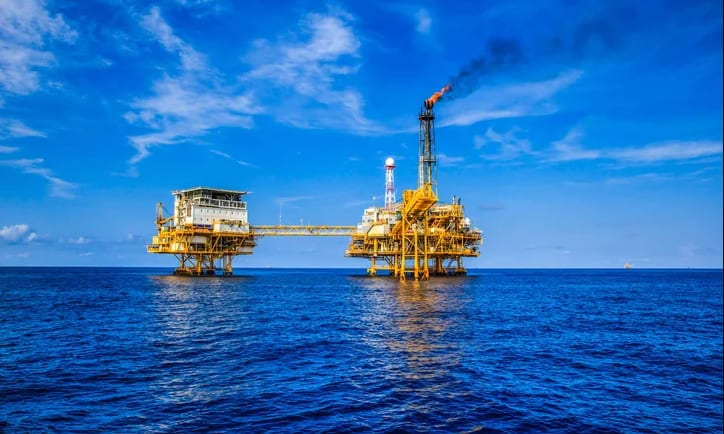
Energy Sector - Oil Drilling Rig
Drive drill pipe rotation and wellhead blowout preventer control.
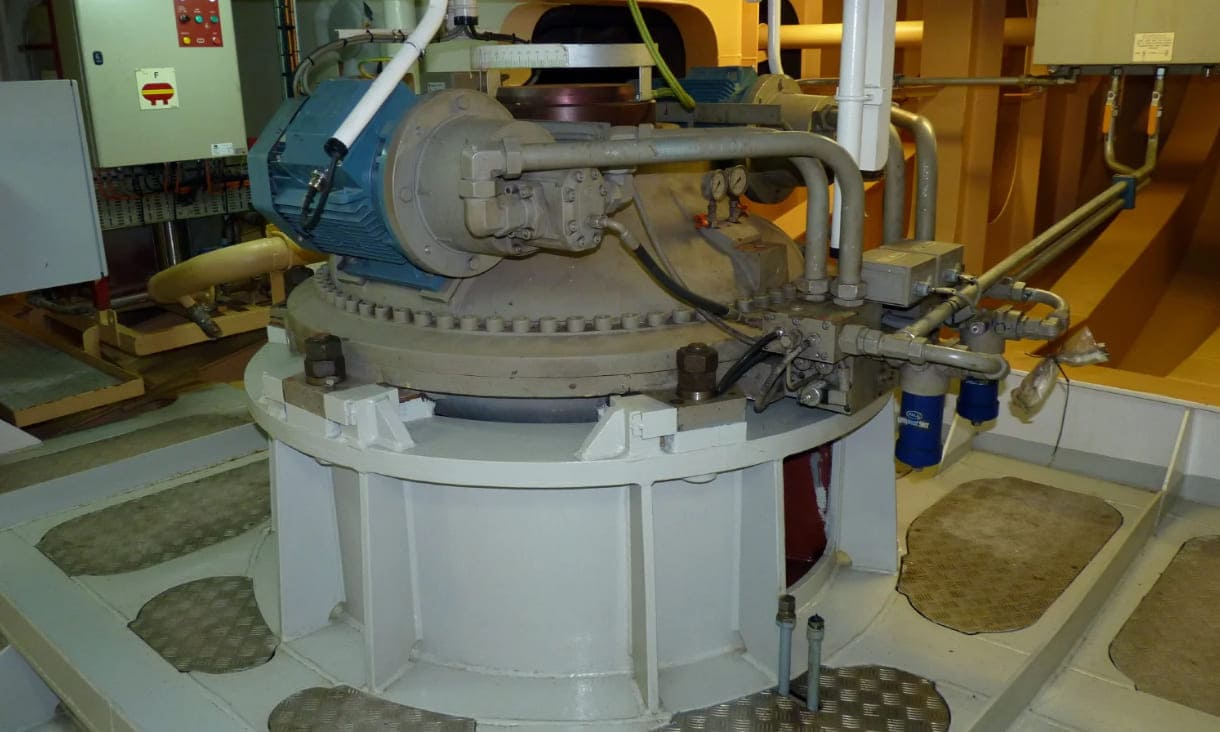
Marine & Offshore Engineering - Steering Gear System
Control the rudder steering to ensure the direction of navigation.
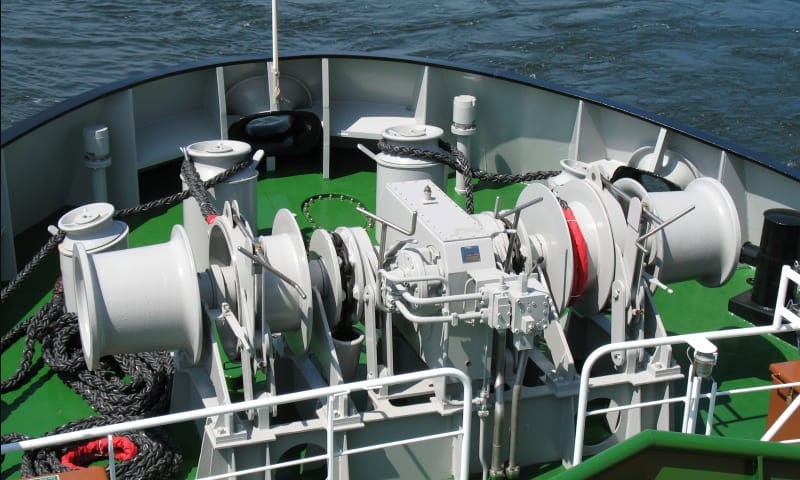
Marine & Offshore Engineering - Anchor Windlasse
Achieve anchor chain retraction and ship positioning.
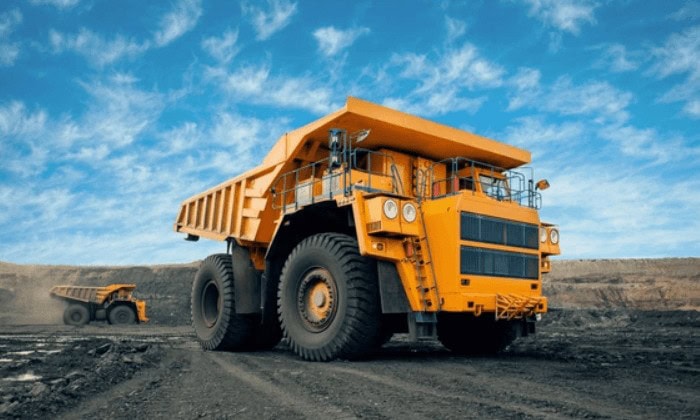
Mining Machinery - Mining Dump Truck
Drive the cargo box lifting hydraulic system to achieve ore unloading.
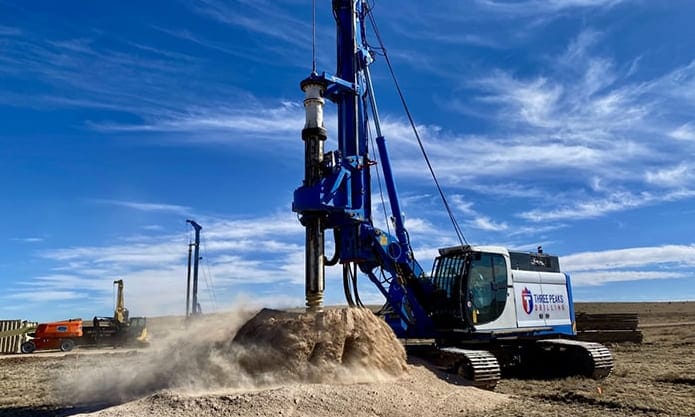
Mining Machinery - Hydraulic Drilling Rig
Provide rotation and feed power for the drill bit.
Tips On How To Maintain And Extend Service Life Of Internal Medium-pressure Hydraulic Gear Pump
Maximizing the lifespan and ensuring peak performance of internal gear pumps in the 16-25 MPa range requires systematic maintenance. Here are key practices supported by industry data and best practices:
1. Regular Inspections and Condition Monitoring
Frequency: Conduct inspections every 500 operating hours or quarterly, whichever comes first.
What to check: Examine gear teeth for wear patterns, pitting, or scoring; check shaft seals and bushings for leakage or wear; inspect pump housing for cracks or corrosion.
Data insight: Studies show that early detection of gear wear can extend pump life by up to 30%, preventing catastrophic failures and costly downtime.
Rotor analogy: Just as brake rotors affect pad performance, worn gears and shafts directly impact volumetric efficiency and pressure stability in pumps.
2. Controlled Start-Up and Running Procedures
Bedding-in equivalent: When commissioning a new pump or after overhaul, run the pump at 50-60% of rated speed and pressure for the first 4-6 hours to allow internal components to seat properly.
Benefits: This reduces initial wear by 25-40% and ensures optimal gear meshing, minimizing leakage and noise.
Operational tip: Avoid sudden pressure spikes or rapid load changes during this period to prevent premature component fatigue.
3. Clean Hydraulic Fluid and Filtration
Fluid cleanliness: Maintain ISO cleanliness code of 18/16/13 or better for hydraulic fluid to prevent abrasive wear.
Filtration: Use high-quality filters with micron ratings ≤10 µm to capture contaminants effectively.
Impact: Contaminated fluid can reduce pump efficiency by 15-20% and shorten service life by up to 50%.
Cleaning caution: Avoid aggressive chemical additives that may degrade seal materials or gear surfaces.
4. Brake Fluid Analogy: Monitor Hydraulic Fluid Condition
Regular testing: Analyze hydraulic fluid every 1000 hours for viscosity, acidity (TAN), and water content.
Recommended parameters: Viscosity should remain within ±10% of manufacturer specs; TAN < 0.5 mg KOH/g; water content < 200 ppm.
Fluid replacement: Replace fluid proactively if parameters deviate to avoid seal swelling, corrosion, or cavitation damage.
Compatibility: Use fluids compatible with internal gear pump materials and operating temperatures (typically mineral oils or synthetic fluids rated for 16-25 MPa systems).
FAQs
Internal meshing gear pumps are more compact, quieter, and have strong self-priming capabilities, making them suitable for scenarios with limited space and low noise requirements (such as medical equipment and food processing); external meshing pumps are lower in cost but have larger flow pulsations, and are mostly used in general industrial equipment.
Yes, by optimizing gear materials (such as powder metallurgy or surface hardening) and sealing technology, the service life can reach more than 10,000 hours, and regular replacement of filters and hydraulic oil can further extend the service life.
The system flow demand (L/min) and working pressure curve need to be calculated, the recommended displacement range is 5-50 cm³/rev, and viscosity compatibility is considered (such as food-grade hydraulic oil requires special sealing materials).
Yes, pumps with fluororubber (FKM) or polytetrafluoroethylene (PTFE) seals are compatible with environmentally friendly oils, but custom designs are required to avoid corrosion and leakage risks.
It provides 316 stainless steel housings, polished flow channels without dead ends, FDA-certified seals, and is designed with CIP (cleaning in place) to meet EHEDG and 3-A hygiene standards.
Yes, its low inertia design and wear-resistant coating can withstand high-frequency start-stop, and is suitable for short-cycle operation scenarios such as logistics sorting machines and automated production lines.
Leakage is mostly caused by seal aging or shaft wear. It is recommended to check the seals every 2000 hours. When the flow rate decreases, it is necessary to check the filter blockage or oil contamination first.
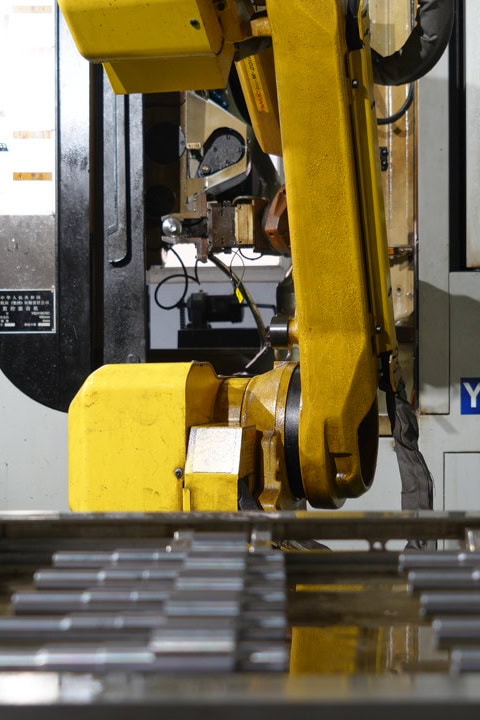
Enpower Your Machine Business Now!
Welcome to consult installation, maintenance and care, after-sales, price and other issues, we will reply you as soon as possible.
Support customization and distributor.