Hydraulic Gear Pump Quality Assurance
Quality Process
Quality control is a key aspect of hydraulic gear pump manufacturing, because the performance and durability of the hydraulic system largely depends on the accuracy and reliability of the gears. Hydraulic gear pump are subjected to high pressure, high temperature and mechanical stress, so ensuring their quality is crucial. The following is a detailed guide to quality control of hydraulic gear pump.
Design and Material Selection
Precision Design: Design gears with precise tooth profiles, pressure angles, and tolerances using CAD software.
Material Selection: Select high-quality materials such as alloy steel, stainless steel, or case-hardened steel to ensure durability and wear resistance.
Heat Treatment: Specify heat treatment processes (e.g., carburizing, nitriding) to enhance hardness and fatigue resistance.
Raw Material Inspection
Material Certification: Verify that the raw materials meet the required standards (e.g., ASTM, DIN, or JIS).
Chemical Composition: Test the chemical composition of the material to ensure it meets the specifications.
Mechanical Properties: Test the raw materials for tensile strength, hardness, and impact.
Manufacturing Process Control
Gear Cutting: Use precision gear cutting machines (e.g., hobbing, planing, or grinding) to ensure accurate tooth profiles.
CNC Machining: Use CNC machines for high-precision manufacturing.
Heat Treatment: Monitor the temperature and time during the heat treatment process to achieve the desired hardness and microstructure.
Surface treatment: Finishing processes such as grinding, honing or polishing are used to reduce surface roughness and improve performance.
Dimensional And Geometric Inspection
Tooth form (involute curve). Tooth pitch (pitch error). Runout and concentricity. Lead and helix angles.
Ensure that gears meet specified tolerances (e.g., AGMA, ISO, or DIN standards).
Measure surface finish to ensure it meets requirements for smooth operation.
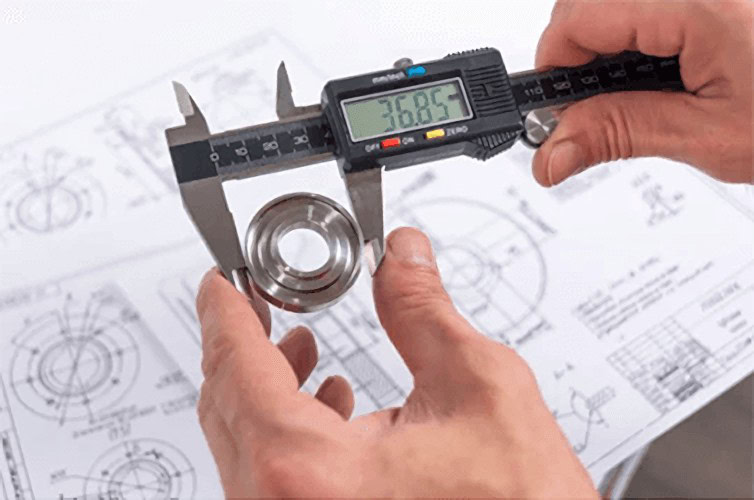
Strict Quality Control System
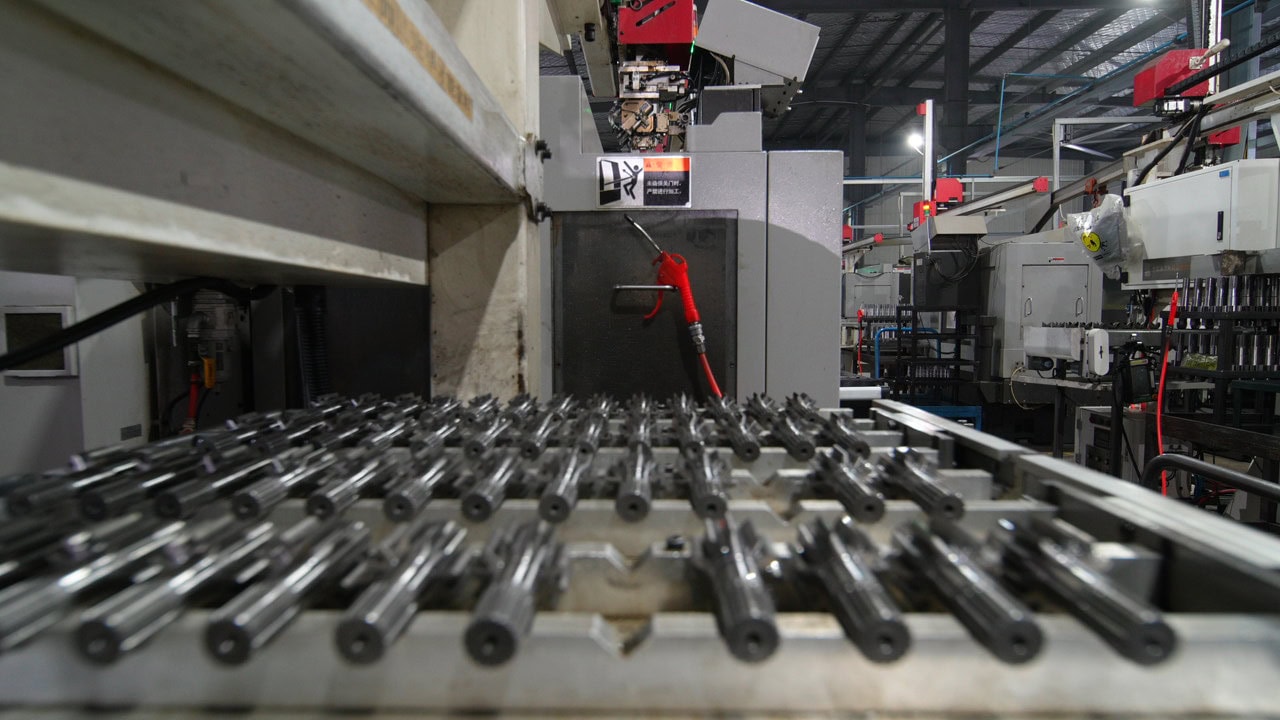
Hardness Test
Surface Hardness: Use Rockwell or Vickers hardness tester to verify the surface hardness after heat treatment.
Core Hardness: Ensure the core hardness is within the specified range to prevent brittleness.
Nondestructive Testing (NDT)
Magnetic Particle Testing (MPI): Detect surface cracks or defects.
Ultrasonic Testing (UT): Identify internal defects or inclusions.
Dye Penetrant Inspection (DPI): Check for surface cracks or porosity.
Performance Testing
Load Testing: Test the gears under simulated operating conditions to evaluate their load-bearing capacity.
Noise and Vibration Testing: Ensure that the gears run quietly and smoothly under load.
Durability Testing: Perform durability testing to evaluate wear resistance and fatigue life.
Quality Documentation
Inspection Report: Keep detailed records of all inspections and tests.
Material Certificates: Keep certificates of raw materials and heat treatment processes.
Traceability: Ensure that each gear can be traced back to its production batch and raw material source.
Let Us See How We Can Help You Quickly.
By implementing a rigorous quality control process, manufacturers can ensure that hydraulic pump gears meet the highest standards of precision, durability, and performance.
If you need more details or assistance, feel free to contact me!